Поточное сверление отверстий во фланцевых заглушках. Историческая справка.
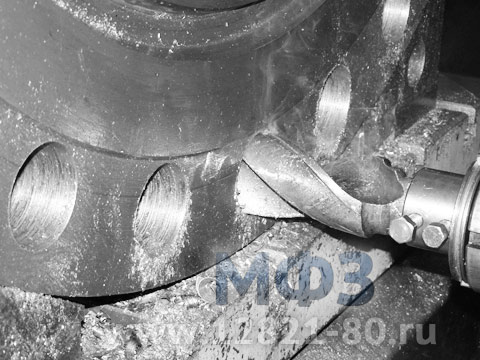
Сверление крепежных отверстий во фланцевой заглушке
Поточное сверление крепежных отверстий во фланцевых заглушках в отечественном серийном производстве 1960-х годов. Многошпиндельный сверлильный станок: назначение, схема, шпиндели, приводы. Станок для зенкования отверстий в заготовках заглушек и фланцев.
Дата публикации: 14 января 2011
Поточная линия по производству заглушек, фланцев и колец из 1960-х
Эта статья продолжает нашу «историческую серию статей» о технологических особенностях давнего производства деталей трубопроводов.
В предыдущих статьях рассказывалось о заготовительном участке производства, где изготавливаются заготовки, а также о точении фланцевых заготовок на токарных станках.
Этап производства, следующий за обточкой заготовок, – сверление отверстий для фланцевых крепежных изделий. На данном этапе производства различие в технологической обработке фланцев и фланцевых заглушек практически не проявляется. Определяющую роль играет количество, диаметр, расположение отверстий под крепеж.
Многошпиндельный сверлильный станок для сверления крепежных отверстий
Назначение станка
Для сверления во фланцах и заглушках отверстий под болты были спроектированы и изготовлены специализированные многошпиндельные сверлильные станки, имеющие по двенадцать рабочих шпинделей.
Общая схема станка для сверления отверстий под крепеж
В основании 1 станка (рис. 1) закреплены четыре колонны 3 — направляющие стола 5 и прижимной плиты 8 и смонтирован пневмогидравлический привод 4, с помощью которого осуществляется подача стола. К прижимной плите крепится сменная кондукторная плита 7, а к верхним концам колонн — многошпиндельная головка 16 станка с электродвигателем 15. Конструкция шпиндельной головки «колокольного» типа дает возможность сверлить четыре, шесть, восемь, десять и двенадцать отверстий, расположенных на окружностях разных диаметров.
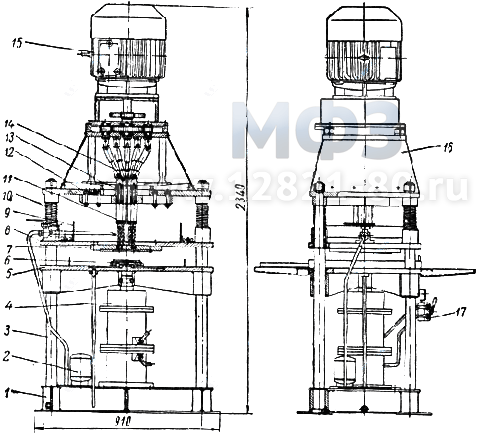
Рис. 1. Многошпиндельный сверлильный станок
для сверления отверстий под болты или шпильки.
Кронштейны 13 и смонтированные в них шпиндели устанавливаются по кондукторной плите (для установки кронштейнов предусмотрены кольцевые пазы, проточенные в основании шпиндельной головки, и продольные пазы в самих кронштейнах), после чего кронштейны крепятся к основанию шпиндельной головки болтами 12. Это упрощает наладку и позволяет устанавливать шпиндели в соответствии с расположением отверстий в обрабатываемых деталях.
Привод шпинделей станка
Шпиндели 11 приводятся в движение через телескопические шарнирные валики 14, вращение которым передается от электродвигателя через шестерни с числом зубьев z1 = 26, z2 = 65, z3=18 и ведущую шестерню z4 (рис. 2).
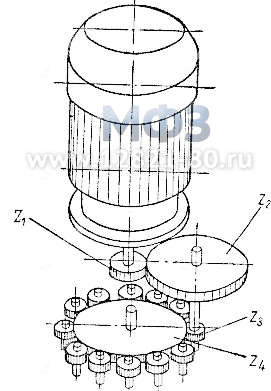
Рис. 2. Схема привода шпинделей станка.
Обработка деталей на станке осуществляется следующим образом. Деталь помещается в установочное приспособление 6 (см. рис. 1), расположенное на столе станка, и подается под кондукторную плиту. Затем включением распределительного крана 17 сжатый воздух подводится в пневмогидравлический привод стола, в результате чего происходит быстрая подача стола, центровка и прижим детали кондукторной плитой 7. Во время сверления отверстий стол, двигаясь вверх с установленной рабочей подачей, благодаря сжатию пружин 10 поднимает прижимную плиту и закрепляет таким образом деталь в процессе обработки. После окончания операции распределительный кран переключается и стол с обработанной стальной заглушкой (или фланцем) быстро отводится в первоначальное положение.
В корпус распределительного крана встроен регулятор давления, позволяющий регулировать величину усилия подачи изменением давления сжатого воздуха, контролируемого манометром.В основании станка предусмотрен резервуар для эмульсии, подаваемой эмульсионным насосом 2 по трубопроводу в зону обработки. В целях безопасности работы на станке на его прижимной плите установлены щитки 9.
Шпиндель станка
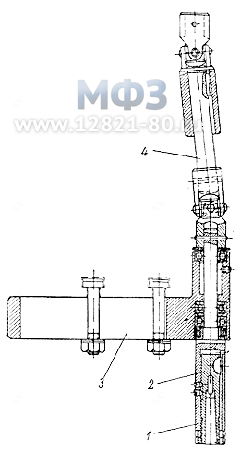
Рис. 3. Шпиндель станка.
На рис. 3 показана конструкция одного из двенадцати шпинделей станка. В кронштейне 3 на двух радиальных шарикоподшипниках смонтирован шпиндель 1, внутри которого имеется сменная оправка 2, позволяющая регулировать положение сверла. Вращение шпинделю передается через шарниры и телескопический валик 4.
Приспособление для подачи деталей под кондукторную плиту
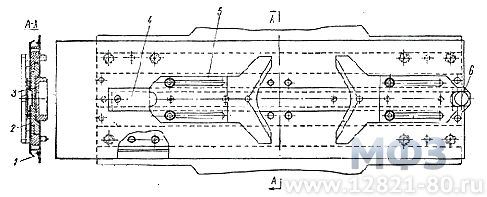
Рис. 4. Установочное приспособление.
На столе станка закреплено приспособление (рис. 4), предназначенное для установки обрабатываемых деталей и подачи их под кондукторную плиту. Деталь устанавливается между двумя призмами 5, которые имеют пазы и могут перемещаться вдоль направляющей 4. Призмы крепятся к ползуну 2, имеющему продольный паз; в него входит втулка 3, вставленная в стол станка.
После установки обрабатываемой детали (фланца стального плоского приварного) ползун подается до совмещения оси детали с центральной осью многошпиндельной головки станка. Во время сверления деталь окончательно центруется сменным кольцом, прикрепленным к кондукторной плите. Обработанную деталь вместе с ползуном выдвигают поворотом ручки 6 и легко снимают с приспособления. От попадания стружки и загрязнения направляющие ползуна защищены двумя щитками 1, закрепленными на ползуне.
Пневмогидравлический привод для подачи стола
Подача стола осуществляется с помощью пневмогидравлического привода (рис. 5). Привод представляет собой сдвоенный пневматический цилиндр, в верхнюю часть которого до определенного уровня залито минеральное масло. На штоке 4, проходящем сквозь уплотнения, имеющиеся в перегородке 2, закреплены поршни 1 и 3. В верхнюю крышку 5 цилиндра ввернут обратный клапан 6 и регулируемый дроссель 7.

Рис. 5. Пневмогидравлический привод.
При работе станка сжатый воздух распределительным краном подается по трубопроводу в полость III и далее по каналу, имеющемуся в штоке, попадает в полость II. В результате шток вместе с закрепленным на нем столом начинает быстро перемещаться вверх. Подъем стола замедляется после того, как манжета, закрепленная на штоке, входит в отверстие верхней крышки, предотвращая дальнейший выход воздуха из полости IV через радиальные отверстия, также имеющиеся в крышке. Шток привода продолжает движение вверх, но со значительно меньшей скоростью, определяемой количеством жидкости, выходящей из полости IV через дроссель. Регулированием дросселя можно устанавливать необходимую для нормальной работы станка рабочую подачу стола. После обработки детали сжатый воздух подводится в полость //, одновременно полости / и /// сообщаются с атмосферой. В результате этого шток привода начинает перемещаться вниз, шарик обратного клапана опускается и пропускает жидкость, скопившуюся в полости V.
Таким образом, подача стола осуществляется по циклу: быстрый подвод — рабочая подача — быстрый отвод. Благодаря простоте и надежности конструкции пневмогидравлический привод обеспечивает бесперебойную работу станка.
Наладка многошпиндельного станка заключается в замене сверл, настройке шпинделей по кондукторной плите и регулировании призм установочного приспособления по детали, центруемой сменным кольцом, закрепленным на кондукторной плите. В кондукторных плитах, устанавливаемых на станке, втулки расположены таким образом, чтобы охватить возможно большее количество типоразмеров обрабатываемых деталей. Это позволяет реже производить замену кондукторных плит.
Сверлильный станок для зенкования отверстий
Заусенцы, остающиеся в отверстиях деталей после сверления на многошпиндельных сверлильных станках, удаляют путем зенкования отверстий на специализированном для этой операции настольно-сверлильном станке модели НС12-АМ (рис. 6). Станок оснащен поворотным столом 2 и пневматическим приводом 4 подачи шпинделя, управляемым с помощью педального распределительного крана 1.
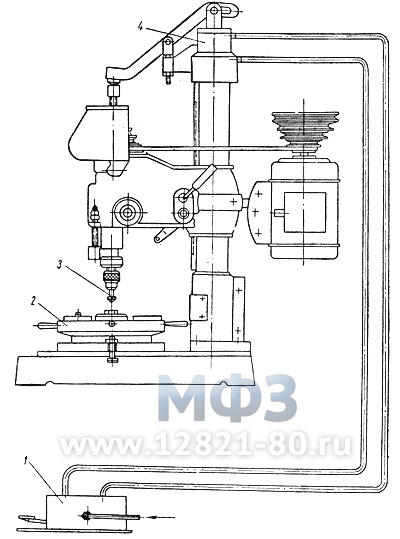
Рис. 6. Станок для зенкования отверстий.
Обрабатываемую деталь устанавливают на поворотном столе, закрепленном на столе станка, так, чтобы ось шпинделя станка совпадала с осью одного из отверстий, просверленных в детали. Затем при нажиме на педаль распределительного крана нижняя полость пневматического привода, расположенного на колонке станка, соединяется с магистралью сжатого воздуха. Происходит подача шпинделя с патроном и закрепленной в нем зенковкой 3 вниз до упора, имеющегося на станке, в результате чего на отверстиях удаляются заусенцы и снимается фаска.
После освобождения педали распределительного крана сжатый воздух поступает в верхнюю полость пневмопривода и шпиндель под действием пружины возвращается в первоначальное положение. После этого верхняя часть стола вместе с трубопроводной деталью поворачивается на определенный угол и цикл повторяется.
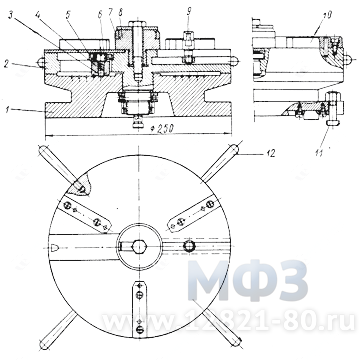
Рис. 7. Поворотный стол.
Поворотная часть 2 стола (рис. 7) установлена на чугунном основании 1, закрепленном двумя болтами 11, входящими в паз стола станка. На поворотной части закреплены три опоры 10, а в отверстие, имеющееся в центре, вставляется сменный центрирующий палец 8. На пальце болтом и быстросъемной шайбой закрепляются сменные кольца 7, которые обеспечивают центрирование деталей внутренним диаметром от 48 до 190 мм, при установке их на столе. В поворотной части стола имеются пазы: в одном из них перемещается сменный установочный палец 9, а в другом — фиксатор 4, закрытый вставленной в поворотную часть планкой 6. В корпусе фиксатора смонтирован 48 стальной шарик 3, постоянно прижимаемый пружиной к оснований стола. Корпус фиксатора может перемещаться вдоль паза и закрепляться гайкой 5. В основании стола имеется пять рядов гнезд, в которые попадает шарик фиксатора при повороте рукояткой 12 верхней части стола. В соответствии с положением фиксатора при повороте стола будет происходить деление окружности расположения центров отверстий под болты на одинаковые части (4, 6, 8, 10 или 12).
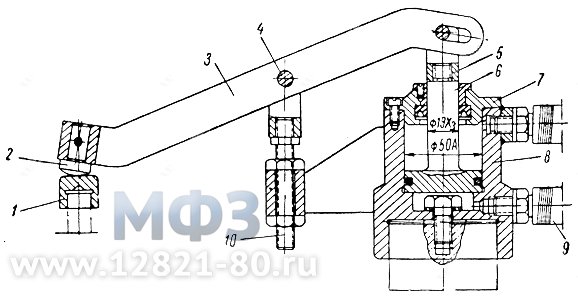
Рис. 8. Привод подачи шпинделя.
Для механизации подачи шпинделя со вставленным в патрон инструментом предусмотрен пневматический цилиндр 8 (рис. 8), закрепленный в верхней части колонки станка болтом и уплотнительной медной шайбой. Шток 6 с помощью вилки 5 шарнирно соединен с рычагом 3, на другом конце которого имеется упор 2, постоянно соприкасающийся с каленым колпачком 1, установленным на шпинделе станка.
Подача шпинделя осуществляется следующим образом: сжатый воздух направляется по шлангу 9 в нижнюю полость цилиндра; при этом поршень с проходящим через крышку 7 штоком начинает перемещаться вверх, поворачивая вокруг оси 4 рычаг, который, нажимая на шпиндель станка, подает его вниз. При поступлении воздуха в верхнюю полость цилиндра рычаг возвращается в первоначальное состояние, а шпиндель поднимается под действием пружины, находящейся в хоботе станка. Величина хода шпинделя регулируется установленной в кронштейне 10 шпилькой.
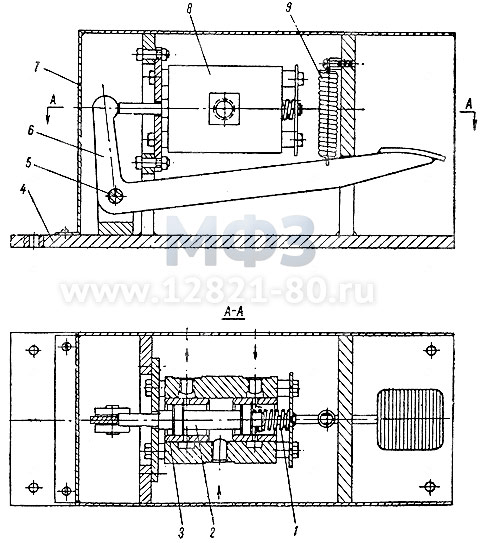
Рис. 9. Педальный распределительный кран.
Устройство, механизирующее подачу шпинделя, управляется педальным распределительным краном (рис. 9). На основании крана 4 смонтирован корпус 8, в который запрессованы стальные каленые втулки 3 с отверстиями, расположенными по окружности.
В корпусе имеются три отверстия:
- к центральному подводится сжатый воздух из магистрали,
- левое соединено с верхней полостью пневматического цилиндра (см. рис. 8),
- а правое – с его нижней полостью.
Цилиндрический золотник 2 под действием пружины 1 постоянно отжимается в крайнее левое положение, обеспечивая подвод сжатого воздуха из магистрали в верхнюю полость пневматического цилиндра. Нижняя полость в этом положении золотника соединена с атмосферой. При нажиме на педаль рычаг 6 поворачивается относительно оси 5, нажимает на выступающий конец золотника и смещает его в крайнее правое положение. При этом верхняя полость пневматического цилиндра сообщается с атмосферой, а в нижнюю подводится сжатый воздух. После освобождения педали рычаг и золотник под действием пружин 1 и 9 возвращаются в исходное положение.
Распределительный кран защищен кожухом 7.
Переналадка станка заключается в замене центрирующего пальца (см. рис. 7) или сменного кольца 7, смене или перестановке установочного пальца 9 и смещении хобота станка в требуемое положение, а также в перестановке фиксатора 4.
После снятия заусенцев готовые фланцы, заглушки и кольца направляются в желоб, являющийся загрузочным устройством автомата, на котором производится маркировка фланцев и колец.
Заключение
Интересные идеи инженеров прошлого можно и нужно применять и в современных условиях высокоразвитого промышленного производства. Человек, обращающийся к своей истории, не сделает многих ошибок, которые он мог по незнанию повторить за предшественниками. А так как инженер – специальность творческая, где же искать источник вдохновения, как ни в достижениях талантливых людей, определявших развитие своего времени.
Список литературы
- Кучер И. М., Кучер А. М. Модернизация и автоматизация станков.. – М. : Машгиз, 1958.
- Митрофанов С. П. Научные основы групповой технологии.. – Л. : Лениздат, 1959.
Получив доступ к данной странице, Вы автоматически принимаете Пользовательское соглашение.