Обработка фланцевой заготовки резанием. Точение фланцев.
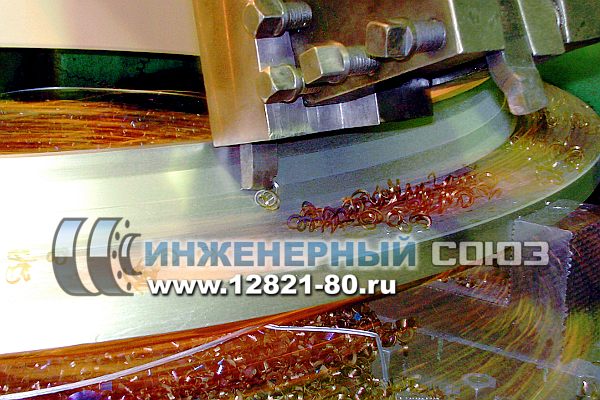
Обработка фланцевой заготовки резанием. Точение воротникового фланца на токарно-карусельном станке.
При производстве фланцев обработка резанием необходима для придания литым или штампованным заготовкам фланцев необходимой формы, размеров, точности и чистоты поверхности. Точение, или обточка, выполняется резцом на токарном станке.
Дата публикации: 13 апреля 2011
Я беру кусок мрамора и отсекаю от него все лишнее
Микеланджело Буонарроти
Важность обработки фланцев резанием
При производстве фланцев обработка резанием необходима для придания литым или штампованным заготовкам фланцев необходимой формы, размеров, точности и чистоты поверхности. Происходит такая обработка путём снятия припуска режущими инструментами на металлорежущих станках. При центробежном литье фланцевая заготовка имеет форму и конфигурацию готового воротникового фланца с припусками на механическую обработку.
Припуск на обработку фланцев
Для того, чтобы получить деталь в окончательно обработанном виде, нужно удалить с заготовки фланца металлический слой, который называется припуском на обработку. Припуск относят к необработанной поверхности и, в основном, берут в расчете на каждую сторону. Но при точении деталей вращения или круглых деталей, таких как фланцы, припуск часто определяют на обе стороны (т. е. на диаметр). Для уменьшения расхода металла и сокращения затрат на механическую обработку припуск должен быть минимальным, но в то же время достаточным для максимально экономичного технологического процесса.
Заготовки фланцев или заглушек, произведенные методом центробежного электрошлакового литья, как правило, имеют КИМ (коэффициент использования металлов) 1,5 – 1,8, поэтому такие воротниковые фланцы имеют минимальные припуски на механическую обработку.
Удаление с заготовки фланца припуска, выполняемое на металлорежущих станках или вручную при слесарной обработке, является механической обработкой. В машиностроении, помимо механического, используются так же другие методы обработки металлов:
- электроискровой,
- анодно-механический,
- химико-механический,
- электрохимический
- ультразвуковой,
где снятие припусков металла происходит под прямым воздействием электрической энергии.
Современное направление обработки фланцев резанием предусматривает полную механизацию, а где это возможно, то частичную или полную автоматизацию методов обработки. В настоящее время на ООО "Инженерный Союз" работают автоматические станочные линии. Рабочими и инженерами производства совместно с омскими учеными ведется работа по модернизации. Имеются опыт и большие достижения в области обработки фланцев резанием.
Методы обработки стальных заготовок фланцев резанием
Заготовки фланцев имеют форму, близкую к форме готовой детали, поэтому подлежат минимальной обработке резанием.
Рис. 1. Виды обработки металлов резанием: а – точение, б – сверление,
в – фрезерование, г – строгание, д – долбление, е – круглое шлифование,
ж – плоское шлифование;
1 – обрабатываемая поверхность, 2 – поверхность резания,
3 – обработанная поверхность.
В зависимости от назначения фланцев и деталей трубопроводов заготовками могут служить отливки, поковки, штамповки, сортовой прокат, сварные заготовки.
В зависимости от формообразования деталей трубопроводов обработка заготовок может выполняться на токарных, сверлильных, фрезерных, строгальных, долбежных, шлифовальных с других станках. Основным методом обработки заготовок фланцев резанием является точение.
Точение фланцев из заготовок
Точение, или обточка, выполняется резцом на токарном станке (рис. 1, а). В процессе обработке заготовке фланца сообщается вращательное движение, а резцу – медленное поступательное перемещение в продольном или поперечном направлении. Оба движения являются движением формообразования фланца. С их помощью на обрабатываемом фланцевом изделии создаются поверхности заданной формы и размеров (воротниковый фланец). При этом движение, производимое с большей скоростью (вращение заготовки фланца), называется главным движением, или движением резания, а более медленное движение, позволяющее охватывать процессом резанием новые, еще не обработанные участки фланцевой заготовки (в данном случае перемещение резца), называется движением подачи. Скорость главного движения называется скоростью резания.
Сверление крепежных отверстий фланцевой заготовки
Сверление отверстий фланцев под крепеж производится на сверлильных станках (рис. 1, б); главное движение вращательное и движение подачи в осевом направлении получает сверло.
Фрезерование заготовок деталей трубопроводов
Фрезерование выполняют на горизонтально-фрезерных станках. Здесь главное вращательное движение получает фреза, а движение подачи в продольном направлении совершает заготовка, закрепленная на столе станка.
Шлифование поверхностей фланцев
Шлифование цилиндрических поверхностей деталей трубопроводов выполняются на круглошлифовальных станках. В этом случае режущий инструмент (шлифовальный круг) получает вращательное движение, заготовка – круговую и продольную подачу, а шлифовальный круг – поперечную прерывистую подачу (рис. 1, е).
При шлифовании уплотнительной поверхности фланца на плоскошлифовальном станке основное вращательное движение сообщается так же шлифовальному кругу (рис. 1, ж). Поперечно-прерывистую и продольную подачи совершает заготовка, а вертикальную прерывистую подачу производит шлифовальный круг.
Основы резания фланцевой заготовки токарным резцом
Рис. 2. Составные элементы резца
Элементы и углы резца
Принцип функционирования любого режущего инструмента основывается на действии клина. Рассмотрим, например, элементы и геометрические характеристики такого режущего инструмента, как токарный резец.
Основные элементы резца
Резец включает в себя (рис. 2):
- рабочую часть – головку, которая непосредственно принимает участие в отделении срезаемого слоя металла,
- нижнюю опорную поверхность – подошву, на которую опирается резец при установке на станке,
- тело (стержень), с помощью которого резец закрепляется в резцедержателе.
Основными элементами резца являются (рис. 2):
- передняя поверхность 1, по которой сходит стружка;
- главная задняя поверхность 3, обращенная к поверхности резания;
- вспомогательная задняя поверхность 4, обращенная к обработанной поверхности;
- главная режущая кромка 2, являющаяся пересечением передней и главной задней поверхностей;
- вспомогательная режущая кромка 5, являющаяся пересечением передней и вспомогательной задней поверхностей,
- вершина 6.
Углы резца
Для идентификации углов резца стандартами установлены следующие понятия (рис. 3):
- плоскость резания,
- основная плоскость,
- главная секущая плоскость.
Для удобства определения некоторых углов режущего клина целесообразно ввести дополнительное понятие – нормальная плоскость.
Плоскостью резания 1 (рис. 3) называется плоскость, косательная к поверхности резания и проходящая через главную режущую кромку.
Основной плоскостью 2 называется плоскость, параллельная направлению продольной и поперечной подачи. У токарных резцов основная плоскость совпадает с нижней опорной поверхностью резца.
Нормальную плоскость определяют как плоскость, проходящую через главную режущую кромку и перпендикулярную плоскости резания.
Рис. 3. Определяющие плоскости резца. 1 – плоскость резания;
2 – основная плоскость; 3 – нормальная плоскость;
4 – главная секущая плоскость; 5 – обрабатываемая поверхность;
6 – поверхность резания; 7 – обрабатываемая поверхность.
Главной секущей плоскостью 4 называется плоскость, перпендикулярная к проекции главной режущей кромки на основную плоскость.
Как видно из рисунка 3, б, в и г, характер поверхности резания и положение ихсходных плоскостей меняются в зависимости от типа режущего инструмента и направления подачи.
Рис. 4. Углы резца и их назначение
Различают главные и вспомогательные углы, а так же углы в плане. Главные углы измеряются в главной секущей плоскости (рис. 3). К ним относятся: главный задний угол, угол заострения, главный передний угол и угол резания.
Главный задний угол α – угол между плоскостью резания и главной задней поверхностью. Этот угол необходим чтобы уменьшить силу трения между обрабатываемым фланцем и резцом. Практически угол α составляет от 6 до 12°.
Главный передний угол γ – угол между передней поверхностью и нормальной плоскостью. Величина переднего угла влияет на процесс стужкообразования. Угол γ составляет от +25 до – 10°.
Угол заострения β – угол между передней поверхностью и главной задней поверхностью. Чем больше этот угол, тем прочнее режущая часть инструмента и тем лучше условия отвода теплоты трения от режущей кромки.
Угол резания δ – угол между плоскостью резания и передней поверхностью, он выражается через:
δ = α + β =90° – γ.
Угол при вершине резца ε – угол между проекциями главной и вспомогательной режущих кромок на основную плоскость.
Главный угол в плане φ – угол между проекцией главной режущей кромки на основную плоскость и направлением подачи.
Вспомогательный угол в плане φ1 – угол между проекцией вспомогательной режущей кромки на основную плоскость и направлением подачи.
Вспомогательный задний угол α1 (измеряют этот угол во вспомогательной секущей плоскости) – угол между 1) вспомогательной задней поверхностью и вертикальной плоскостью, проходящей черезвспомогательную режущую кромку и 2) плоскостью, перпендикулярной к основной.
Угол наклона главной режущей кромки λ – угол между главной режущей кромкой и основной плоскостью.
Заключение
Обработка заготовок резанием – одна из последних технологических операций в производстве деталей трубопроводов. Особой точности обработки требуют уплотнительные поверхности фланцев. Важность точности сверления отверстий возрастает с ростом Ру фланцев, так как малейшие отклонения в диаметре или расположении центров отверстий приводят к резкому возрастанию нагрузки в отдельно взятых шпильках или болтах.
Список литературы
- Батышев А. И. Проектирование и производство заготовок / А. И. Батышев. – 2-е изд., испр. и доп.. – М.: Изд-во МГОУ, 2005. – 108 c.
- Технология металлов и сварка / под ред. П. И. Полухина.. – М. : Высшая школа, 1968.
- Токарные многошпиндельные автоматы.. – М.: Машиностроение, 1978. – 309 c.
- Аршинов В. А., Алексеев Г. А. Резание металлов и режущий инструмент. – Изд-е 2-е. – М. : Машиностроение, 1968.
- Соколов С. П. Тонкое шлифование и доводка.. – Л. : Машгиз, 1961.
Получив доступ к данной странице, Вы автоматически принимаете Пользовательское соглашение.