Автоматический станок для маркировки фланцев
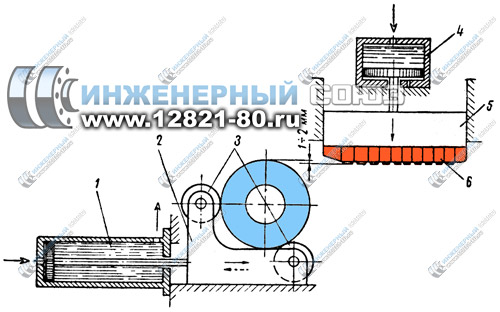
Схема маркировки фланцев, заглушек, приварных колец и др. деталей трубопроводов.
Устройства для автоматической маркировки деталей трубопроводов, используемые на предприятиях с поточным технологическим процессом, должны производить маркировку четко, быстро и в соответствии со стандартами. В данной статье описывается автоматический станок для маркировки готовых изделий, его устройство и технические характеристики.
Дата публикации: 22 января 2011
Содержание
Механический маркировочный автомат
Устройство и технологический процесс маркировочного автомата
Согласно требованиям ГОСТ, на наружной цилиндрической поверхности фланцев стальных плоских и колец должна быть нанесена маркировка. Зачастую на отечественных предприятиях детали трубопроводов маркируют вручную или с помощью простейших приспособлений; это весьма трудоемкая операция, не обеспечивающая надлежащей точности, скорости и автоматизации.
На предприятиях, где налажено поточное производство, необходим автоматизированный способ нанесения маркировки, например, используется механический маркировочный полуавтомат, который путем установки загрузочного устройства может быть переоборудован в автомат, функционирующий без участия рабочего.
В данной особое внимание уделим механическому способу нанесения маркировки.
Механический маркировочный автомат
Рис. 1. Схема процесса маркировки фланцев, заглушек,
приварных колец и др. деталей трубопроводов.
Механический маркировочный автомат имеет высокую производительность и полностью устраняет ручной труд при изготовлении фланцев и приварных колец. Процесс маркировки происходит методом накатывания цифр и букв на наружную цилиндрическую поверхность деталей. Деталь, подлежащая маркировке, из загрузочного устройства попадает на опорные ролики 3 (рис. 1), установленные в каретке 2.
При движении вправо с помощью гидроцилиндра 1 каретка совершает рабочий ход. Лежащая на роликах деталь (ей может также являться фланец стальной приварной встык) благодаря наличию заборной части у кассеты 5 входит в соприкосновение с вставленными в нее клеймами 6 и начинает вращаться, так как суппорт с закрепленной в нем кассетой прижимается к детали с помощью гидроцилиндра 4. Все это обеспечивает получение четкого оттиска на наружной цилиндрической поверхности маркируемой детали имеющихся на клеймах букв и цифр.
↑ В начало
Клейма для маркировки
Рис. 2. Набор клейм для маркировки фланцев и других
деталей трубопроводов.
Клейма 2 (рис. 2), с помощью которых осуществляется маркировка стальных фланцев, набираются между двух планок 1 и 3, соединенных штырями 4, проходящими сквозь отверстия, имеющиеся в клеймах. Набор клейм должен заполнять всю обойму; если количество клейм меньше максимального, то набор дополняется брусками, не имеющими гравировки.
↑ В начало
Устройство и технологический процесс маркировочного автомата
На рис. 3 показана конструкция автомата для маркировки деталей. Станина станка 16 представляет собой сварной каркас, на котором под углом 40° к горизонтальной плоскости размещен стол 12. Наклонное положение стола обеспечивает подачу деталей, подлежащих маркировке, из загрузочного устройства к рабочим органам станка под действием собственного веса. Внутри станины расположен гидропривод автомата, состоящий из смонтированных на общей раме электродвигателя 17 мощностью 2,8 кВт и шестеренчатого насоса 18 производительностью 35 л/мин. Рабочая жидкость — масло — подается к насосу из масляного бака 19, установленного в нижней части станины.
Рис. 3. Автомат для маркировки деталей.
На столе станка имеются направляющие, по которым могут перемещаться два суппорта: 2 и 21. Посредством суппорта производится перемещение кассеты 23 с клеймами, что необходимо для маркировки деталей разных диаметров.
Постоянный прижим клейм к поверхности детали осуществляется с помощью гидроцилиндра, расположенного внутри станины и надежно закрепленного на нижней стороне стола. Регулировочный винт 1 проходит через гайку суппорта 2 и соединяется со штоком гидроцилиндра так, что имеет возможность свободно вращаться, перемещая суппорт, как схематично показано на рис. 4.
На суппорте 21 находится линейка 22; образующийся между нею и суппортом 2 лоток используется для подачи обрабатываемых деталей на маркировку. В зависимости от размера деталей суппорт 21 вместе с линейкой может перемещаться винтом 20, образуя лоток необходимой ширины.
В продольных направляющих стола с помощью гидроцилиндра 15, смонтированного на торце стола, перемещается каретка 10, несущая два ползуна 9, в которых установлены опорные ролики 7. На одном из ползунов закреплен отсекатель 13, задерживающий очередной фланец в загрузочном лотке. Ползуны с роликами устанавливаются в зависимости от размеров маркируемых деталей и надежно закрепляются на каретке. На ползунах имеются упоры 8 и 11, а на столе – золотники гидравлические 6 и 14.
В крайнем левом положении (на виде А — крайнее верхнее положение) каретки происходит загрузка детали.
Перемещаясь под действием собственного веса по наклонному лотку, деталь попадает на ролики. Одновременно упор 11 нажимает на золотник 14, с помощью которого осуществляется реверсирование хода каретки, перемещающейся гидроцилиндром.
При движении каретки вправо (на виде А – вниз), обрабатываемая деталь входит в соприкосновение с клеймами, закрепленными в кассете, – происходит маркировка. При дальнейшем движении каретки вправо фланец снимается съемником 5 и прижимается к нему прижимом 4, сталкивая обработанную ранее деталь в наклонный лоток, по которому она поступает в ванну для консервации. В то же время упор 8 нажимает на золотник 6, благодаря чему происходит реверсирование хода каретки и возврат ее в загрузочное положение. Таким образом, каретка непрерывно совершает возвратно-поступательное движение.
С пальцем прижима связан рычаг счетчика 3, отсчитывающих количество деталей, изготовленных на поточной линии. На станине станка размещены пусковая кнопочная станция, электрощит и щит управления станком.
↑ В начало
Гидравлическая схема работы маркировочного станка
Рис. 4. Автомат маркировки готовой трубопроводной продукции.
Надежная работа автомата, обеспечивается гидравлической схемой, показанной на рисунке 4. Из масляного бака рабочая жидкость нагнетается в систему шестеренчатым насосом 1 типа Ш-35, проходит через кран управления 3 и поступает в верхнюю полость гидроцилиндра 11, обеспечивающего постоянный прижим кассеты 10 с клеймами к маркируемой детали. Одновременно жидкость подводится к реверсивному золотнику 4 с гидравлическим управлением, которое осуществляется двумя золотниками 8 и 13, соответственно срабатывающими от нажима упоров 9 и 12.
Во время рабочего хода каретки с маркируемой деталью (положение, показанное на рис. 4) реверсивный золотник находится в крайнем правом положении, обеспечивая поступление жидкости через дроссель 5 в левую полость рабочего гидроцилиндра 7; при этом шток цилиндра и связанная с ним каретка перемещаются вправо. Правая полость гидроцилиндра в этот момент соединена с баком. Обе переключающие полости реверсивного золотника 4 через золотники 8 и 13 также соединены с баком. Перемещаясь вправо, упор 12, закрепленный на каретке, нажимает на золотник 13, после чего правая полость реверсивного золотника 4 сообщается с системой. Поскольку левая полость соединена с баком, то реверсивный золотник перемещается в крайнее левое положение, соединяя правую полость гидроцилиндра с системой, а левую — с баком. В результате этого переключения каретка, освобожденная съемником от маркируемой детали, начинает двигаться влево, совершая холостой ход. Скорость холостого хода каретки значительно больше скорости рабочего хода благодаря наличию обратного клапана 6. Холостой ход продолжается до момента, когда упор 9 нажмет на золотник 8, переключая систему на рабочий ход.
Таким образом, рабочие и холостые ходы каретки чередуются непрерывно, пока открыт кран. Постоянство давления жидкости в системе и предохранение последней от перегрузок обеспечивается предохранительным клапаном 2.
Наружный диаметр маркируемых деталей, мм | наименьший | 55 |
наибольший | 310 | |
Максимальная длина маркировки, мм | 170 | |
Производительность, шт/час | 600 | |
Мощность электродвигателя, кВт | 2,8 | |
Габариты станка, мм | 1300X800X1050 | |
Масса станка, кг | 600 |
↑ В начало
Заключение
Стандарты на стальные фланцы (фланцы ГОСТ 12820-80, ГОСТ 12821-80 и др.) предписывают производить маркировку изделий, другие детали трубопроводов также нуждаются в маркировке. Устройства для автоматической маркировки, используемые на предприятиях с поточным технологическим процессом, должны производить маркировку четко, быстро и в соответствии со стандартами.
Описанный здесь станок – уже дань истории, хотя его характеристики позволяют эксплуатировать его и по сей день. Более современные средства маркировки основываются на лазерных технологиях.
Список литературы
- Кучер И. М., Кучер А. М. Модернизация и автоматизация станков.. – М. : Машгиз, 1958.
- Бржезяк Ю. Д. Пневматические и пневмогидравлические зажимы в приспособлениях.. – Л. : Судпромгиз, 1957.
Получив доступ к данной странице, Вы автоматически принимаете Пользовательское соглашение.