Классификация способов и сущность процесса сварки соединительных деталей трубопроводов
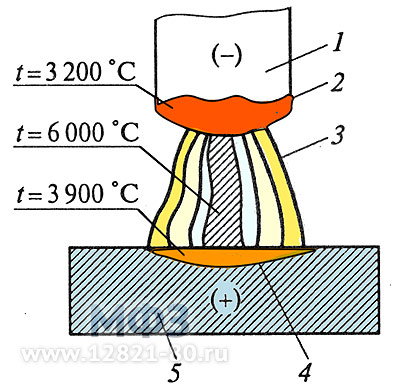
Схема электродуговой сварки
Классификация способов и сущность процесса сварки соединительных деталей трубопроводов. Сварка плавлением и сварка давлением. Энергия для сварки: электрическая, механическая, химическая, лучевая сварка. Физические процессы при электрической дуговой сварке фланца и трубы. Образование сварного соединения. Типы электродов для сварки труб и деталей трубопроводов и их назначение.
Дата публикации: 12 января 2011
Содержание
1. Краткая классификация сварки
1.3. Подача пересадочного металла и флюсов к месту сварки
Краткая классификация сварки
Способы сварки
Сварка представляет собой процесс получения неразъемных соединений металлических деталей в узлы и конструкции (приварные фланцы и стальные трубы). По своей природе сварка является сложным и разнообразным металлургическим процессом. Образование сварных фланцевых соединений и узлов происходит в большинстве случаях в узкой зоне плавления соединяемых деталей трубопроводов с последующей кристаллизацией этих зон и образованием сварочного шва.
Широкое применение сварки объясняется ее технико-экономическими преимуществами (снижение стоимости продукции, снижение стоимости узлов соединительных деталей трубопроводов за счет возможности отказа от крепежных деталей, экономия металла и сокращение производственного цикла) по сравнению с другими способами соединения металлических деталей. Например, при переходе от клепанных конструкций к сварным, к замене тяжелых литых деталей более легкими – сварными. Сварка позволяет получать рациональные конструкции, используя различные профили сортового проката. Большую экономию дает также использование сварки при ремонтных работах, восстановление изношенных деталей и исправление брака отливок фланцев.
Принято все существующие способы сварки делить на две большие группы:
- сварка плавлением и
- сварка давлением.
Сварка плавлением характеризуется соединением частей металла в жидком состоянии без приложения давления. При сварке давлением соединение частей металла в единое целое происходит под действием давления для осадки металла, остальные признаки, в том числе состояние металла, не принимаются во внимание. Приложение давления даже при наличии расплавления в зоне сварки позволяет отнести способ к группе сварки давлением, например, при электрической контактной сварки (точечной и роликовой шовной для соединительных деталей трубопроводов).
↑ В начало
Энергия для сварки
Сварка, кроме того, подразделяется по виду энергии, используемой для нагрева металла при сварке. По этому признаку все способы сварки можно объединить в четыре основные группы:
- электрические,
- механические,
- химические и
- лучевые.
↑ В начало
Подача пересадочного металла и флюсов к месту сварки
В зависимости от способа подачи пересадочного металла и флюсов к месту сварки, осадки деталей и управление источником теплоты различают способы сварки:
- ручной,
- полуавтоматический и
- автоматический.
В промышленности, в частности при производстве сварных труб, а так же в строительстве – при прокладке трубопроводных магистралей, наибольшее применение нашла электросварка, использующая электрическую энергию для нагрева и плавления металла соединяемых деталей трубопроводов.
В механических способах сварки преобладающее значение имеет механическая энергия, которую используют при холодной, прессовой, кузнечной сварке, а так же сварке трением.
При химических способах сварки для нагрева металла используется энергия экзотермических химических реакций, из которых наибольшее значение имеют газовая и тернитная.
Сварка лучевая, или диффузионная, обеспечивает высокую частоту процесса, в которой источник энергии расположен на значительном расстоянии от объекта сварки. К лучевым относятся такие способы сварки, как электронно-лучевая, лазерная и другие.
↑ В начало
Процесс сварки
Соединение, полученное в результате сварки характеризуется непрерывной структурной связью и монолитностью строения, достигаемыми за счет образования атомно-молекулярных связей между элементарными частицами соединяемых деталей трубопроводов. Неразъемное монолитное соединение, называется сварным соединением.
Процесс образования соединения при сварке происходит в три стадии.
- На первой стадии достигается физический контакт (между приварным фланцем и стальной трубой), то есть осуществляется сближение соединяемых веществ на расстояния, необходимые для межатомного взаимодействия.
- На второй стадии происходит химическое взаимодействие, которое заканчивается процессом образования прочного соединения фланца и трубы. Эти две стадии характерны для микроучастков соединяемых веществ.
- Процесс сварки трубы и фланца завершается диффузией.
Для качественного соединения деталей трубопроводов необходимо обеспечить контакт значительной части стыкуемых поверхностей и их активацию. Активация состоит в том, что поверхностным атомам твердого тела сообщается некоторая кинетическая энергия, необходимая для преодоления связей между ними и повышение энергии поверхностных атомов до уровня энергетического барьера схватывания, то есть для перевода их в активное состояние. Такая энергия может быть сообщена в виде теплоты (термическая активация) и других видов воздействия на соединяемые материалы.
Рис. 1. Схема сварного соединения при сварке плавлением:
а – соединяемые детали:
слева – соединение плоского фланца с трубой;
справа – соединение фланца воротникового (приварного встык) с трубой;
б – сварочная ванна;
в – кристаллизация расплава; г, д – структуры шва;
Q – поток тепловой энергии.
При сварке плавлением образование сварного соединения стального воротникового фланца и плоского фланца со стенкой трубы (рис. 1) происходит в результате сближения атомов твердых тел (фланец и стальная труба) вследствие смачивания их поверхностей жидким металлом расплавом, а активация поверхности твердого металла – путем сообщения ее частицам тепловой энергии. Металл элементов соединяемых деталей трубопроводов (рис. 1, а) в месте сварки доводится под водимой тепловой энергии Q до жидкого состояния. При этом происходит локальное расплавление и основного свариваемого металла деталей трубопроводов по кромкам соединяемых элементов. Сварка может осуществляться за счет расплавления основного металла или основного и дополнительного присадочного металлов. В практике преимущественное применение находит второй вариант. В процессе сварки основной и дополнительный металлы самопроизвольно и без приложения внешних сил сливаются в общую сварочную ванну (рис. 2, б), которая смачивает оставшуюся твердую поверхность соединяемых элементов трубопроводов. При этом происходит сближение атомов металла сварочные ванны и основного металла до расстояний, при которых возникают атомно-молекулярные связи.
По мере удаления источника нагрева расплав остывает и происходит кристаллизация (рис. 1, в), которая начинается на границе раздела между твердым основным металлом и расплавом сварочной ванны. Зародышевыми центрами кристаллизации являются оплавленные зерна основного металла, на которых, как на своеобразной подложке, начинают расти первичные столбчатые кристаллы сварочного шва. Кристаллы растут по нормали к поверхности охлаждения в глубь жидкой ванны и имеют вид дендритов разной величины.
При сравнительной малой величине сварочной ванны образующиеся столбчатые кристаллы успевают прорасти до встречи друг с другом в области центральной линии сварного шва (рис. 1, г). Когда сварочная ванна большая и ее кристаллизация медленная, в центральной части сварного шва появляется небольшая зона равноосных кристаллов (рис. 1, д).
После завершения кристаллизации сварочной ванны образуется монолитный, имеющий литую структуру шов, соединяющий в единое целое ранее раздельные детали трубопроводов.
↑ В начало
Электрическая дуговая сварка
Электрическая дуговая сварка – важнейший промышленный вид сварки металлов, занимающий первое место по числу оборудования и вовлеченного персонала предприятий.
Рис. 2. Схема электрической сварочной дуги:
1 – электрод (является катодом, "–");
2,4 – анодное и катодное пятна;
3 – столб электрической дуги;
5 – изделие (соединение трубы с фланцем,
заглушкой, переходом, тройником и т.д.).
Электрическая сварочная дуга – мощный временной электрический разряд между проводниками в ионизированной атмосфере газов и паров металла, который сопровождается выделением большого количества теплоты и света.
Сварочная дуга на постоянном токе (рис. 2) включает катодное пятно 2, которое образуется на электроде 1, столб 3 дуги и анодное пятно 4 на изделии (анод, "+"). При изменении полярности изделие становится катодом, а электрод – анодом. Для дуги переменного тока характерно постоянное периодическое изменение полярности с частотой переменного тока.
Для появления и горения дуги необходимо наличие в промежутке между электродом и изделием заряженных ионов, которые в воздухе обычного состояния отсутствуют. Ионная проводимость воздуха появляется при контакте электрода с изделием. Электрическая цепь при этом замыкается и из-за короткого замыкания происходит разогрев электрода. После отведения электрода на некоторое расстояние от поверхности изделия начинается термоэлектрическая эмиссия электронов с поверхности анода. Столкновение разогнанных в электрическом поле электронов с молекулами газов и паров металла приводит к желаемой ионизации промежуточного пространства. При разогреве происходит дополнительная ионизация, в результате возникает стойкий дуговой электрический разряд.
Высокая температура и значительная энергия сварочной дуги дают возможность быстро расплавлять небольшие объёмы металла свариваемых деталей.
Энергия из сварочной дуги выделяется неравномерно. На аноде ("+") выделяется около 43% теплоты вследствие его бомбардировке электронами, имеющими более высокую кинетическую энергию по сравнению с ионами. На катоде ("–") выделяется около 36% теплоты. Остальная тепловая энергия рассеивается в окружающем пространстве.
Распределение температуры в дуге указано на рисунке 2.
Обычно с электрода в сварочную ванну в виде капель стекает вплоть до 90% металла электрода, остальной же металл не достигает сварочной ванны в результате окисления, разбрызгивания и испарения.
Устойчивое горение дуги, необходимое для высокого качества сварки, достигается при ее длине 3…5 мм. Длину, на которую проплавляется свариваемый металл, называют глубиной сварки.
↑ В начало
Сварочные материалы
Сборка магистральных трубопроводов выполняется с применением ручной, полуавтоматической и автоматической электрической сварки.
Для этих целей применяются следующие материалы:
- электроды различных марок,
- флюсы и
- сварочная проволока.
Рассмотрим требования к их качеству.
Для автоматической газоэлектрической сварки стыков труб применяются:
- сварочная проволока с омедненной поверхностью по ГОСТ 2246-79;
- углекислый газ по ГОСТ 8050-85 (двуокись углерода газообразная);
- аргон газообразный по ГОСТ 1057-79;
- смесь из углекислого газа и аргона.
Для автоматической сварки стыков труб под флюсом применяются флюсы по ГОСТ 9087-81 и проволока углеродистая или легированная преимущественно омедненной поверхностью по ГОСТ 2246-70. Марки флюсов и проволок выбираются в соответствии с технологическими инструкциями в зависимости от назначения и нормативного сопротивления разрыву металла свариваемых труб.
Для механизированной сварки стыков труб, или сварки труб и фланца применяются порошковые проволоки, марки которых выбираются в соответствии с технологическими инструкциями.
Для ручной электродуговой сварки стыков трубопроводов или фланца и участка трубы применяются электроды с целлюлозным (Ц) и основным (Б) видами покрытий по ГОСТ 9466-75 и ГОСТ 9467-75.
В таблице 6.4 приводятся рекомендации по выбору типа электродов.
Для газовой резки труб применяются:по
- кислород технический по ГОСТ 5583-78;
- ацетилен в баллонах по ГОСТ 5457-75;
- пропан-бутановая смесь по ГОСТ 20448-90.
Таблица 1. Типы электродов применяемых при сварке трубопроводов (фланца и трубы).
Нормативное значение (по ТУ) временного сопротивления разрыву металла труб, 102 МПа (кгс/мм2) | Назначение электрода
| Тип электрода (по ГОСТ 9467-75) - вид электродного покрытия (по ГОСТ 9466-75) |
До 5,5 (55)
| Для сварки первого (корневого) слоя шва неповоротных стыков труб | Э42-Ц
|
До 6,0 (60) включ. | Э42-Ц, Э50-Ц | |
До 5,5 (55)
| Для сварки «горячего» прохода неповоротных стыков труб | Э42-Ц, Э50-Ц
|
До 6,0 (60) включ. | Э42-Ц, Э50-Ц Э60-Ц | |
До 5,0 (50) включ.
| Для сварки и ремонта сваркой корневого слоя шва поворотных и неповоротных стыков труб | Э42А-Б, Э46А-Б
|
До 6,0 (60) включ. | Э50А-Б, Э60-Б | |
До 5,0 (50) включ.
| Для подварки изнутри трубы
| Э42А-Б, Э46А-Б
|
До 6,0 (60) включ. | Э50А-Б | |
До 5,0 (50) включ.
| Для сварки и ремонта заполняющих и облицовочного слоев шва (после «горячего» прохода электродами Ц или после корневого слоя шва, выполненного электродами Б) | Э42А-Б, Э46А-Б
|
От 5,0 (50) До 6,0 (60) включ. Для сварки | Э50А-Б, Э55-Ц | |
От 5,5 (55) до 6,0 (60) включ. | Э60-Б, Э60-Ц, Э70-Б |
Заключение
Сварка имеет значительную, а в некоторых случаях, и решающую роль в процессе строительства трубопроводов, производства деталей трубопроводов и их сборки. Успешные инновации в этой области производства приводят к заметному снижению себестоимости строительства, технического обслуживания и ремонта трубопроводов и их элементов.
↑ В начало
Список литературы
- Чернышов Г. Г. Сварочное дело: Сварка и резка металлов / Г. Г. Чернышов.. – М. : Изд. центр «Академия», 2004.
- Технология металлов и сварка / под ред. П. И. Полухина.. – М. : Высшая школа, 1968.
Получив доступ к данной странице, Вы автоматически принимаете Пользовательское соглашение.