Производство стали и нержавеющих сплавов, фланцев и заглушек методом центробежного электрошлакового литья (ЦЭШЛ)
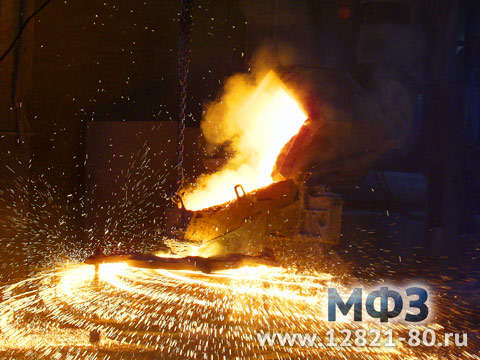
Центробежное электрошлаковое литьё. Залив расплава металла во вращающуюся форму.
Производство стали и нержавеющих сплавов для изготовления воротниковых фланцев, заглушек труб, методом центробежного электрошлакового литья (ЦЭШЛ). Производство стали методом электрошлакового переплава (ЭШП) для изготовления ответственных деталей трубопроводов. Физико-химические процессы в сталях. Центробежное литье кольцевых заготовок воротниковых фланцев.
Дата публикации: 14 января 2011
Содержание
2.1. Физико-химические процессы получения стали.
2.2. Основные компоненты в сталях
2.2.1. Полезные компоненты сталей
3. Электрошлаковый переплав как способ повышения качества стали фланцев.
3.1. Детали трубопроводов и фланцы высокого давления, больших диаметров.
4. Центробежное литье кольцевых заготовок воротниковых фланцев
Общие сведения
Производство металлов и сплавов на их основе связано с металлургией. Металлургия – наука о промышленных способах получения металлов и сплавов, заключающихся в извлечении металлов из природных соединений (железные руды) и дальнейшей их обработке с целью придания полученному металлу определенной формы (в нашем случае фланцы и заглушки труб, другие элементы трубопроводов методом ЦЭЩЛ) и необходимых свойств (например фланцы нержавеющие). Производство сплавов на основе железа (стали нержавеющие и углеродистые) и их дальнейшую переработку – литье, штамповку, ковку и др., производят, получают и обрабатывают на металлургических предприятиях.
↑ В начало
Производство стали для изготовления ответственных деталей трубопроводов. Фланцы, заглушки, прокладки, переходы, тройники
Физико-химические процессы получения стали.
Сталь по сравнению с чугуном содержит меньшее количество углерода и, как правило, имеет пониженное содержание кремния, марганца, фосфора и серы. Для получения стали из чугуна необходимо снизить содержание этих элементов путем окислительной плавки, проводимой в сталеплавильных агрегатах.
Одним из экономичных способов производства стали является плавка в электрических печах. Для выплавки стали используются следующие исходные материалы:
- металлошихта (лом),
- металлодобавки,
- флюсы и
- окислители.
Основная масса металлошихты – стальной лом. В состав металлошихты могут входить так же продукты прямого восстановления железа из руд и ферросплавы.
Металлодобавки в виде ферросплавов вводятся в сталь для ее раскисления и легирования.
Флюсами (добавочными материалами) являются известняк, боксит и плавиковый шпат. Известняк способствует образованию шлака, а боксит и плавиковый шпат делают его жидкоподвижным.
Для окислительных процессов источником кислорода является газовая среда (кислород, печная атмосфера) или твердые окислители (железная руда, агломерат, окатыши, окалина).
Выбор материала футеровки сталеплавильных агрегатов (тигель при ЭШП) определяется составом и свойствами шлаков, образующихся в процессе плавки. В соответствии с этим различают кислый и основной сталеплавильные процессы, осуществляемые в основных конвертерах, кислых и основных мартеновских электродуговых печах.
Рассмотрим в качестве примера основной сталеплавильный процесс.
Железо при взаимодействии с кислородом окисляется по реакции
(1)
Fe + ½O2 = (FeO)
Газы – окислители печной атмосферы, – взаимодействуя с металлом, окисляют и другие элементы растворенные в металле, в частности:
[Si]* + O2 = (SiO2) | (2) |
[Mn] +½O2 = (MnO) | (3) |
[C] +½O2 = CO | (4) |
Окисление примесей так же может происходить растворенным в металле кислородом:
[Si] + 2 [O] = (Si02) | (5) |
[Mn] + [O] = (MnO) | (6) |
[C] + [O] = CO | (7) |
Элементы с большим химическим сродством к кислороду, чем железо, окисляются оксидом железа, содержащимся в шлаке
[Si] + 2(FeO) = (Si02) + 2[Fe] | (8) |
[Mn] + (FeO) = (MnO) + [Fe] | (9) |
[C] + (FeO) = CO + [Fe] | (10) |
В тигле при ЭШП под шлаком (преимущественно оксид железа и оксид кальция) и при сравнительно невысокой температуре из расплава удаляется фосфор (дефосфоризация металла):
2[P] + 5(FeO) +4(CaO) = (CaO)4 ⋅(P2O5) + 5[Fe] | (11) |
Убирая шлак с поверхности металла (скачивание шлака) и наводя новый (путем подачи флюса требуемого состава), можно удалить значительную часть вредных примесей (серы и фосфора) из металла.
Регулирование состава шлака с помощью флюсов является одним из основных путей управления металлургическим процессом.
Когда окисление примесей почти завершено, начинают образовываться оксиды железа. Растворяясь в стали, они повышают в ней содержание кислорода. Кислород ухудшает прочность и в особенности эластичность и вязкость стали, что способствует появлению трещин при ее пластическом деформировании. Поэтому обязательной завершающей операцией при выплавке стали является ее раскисление, то есть уменьшение содержания в ней кислорода до допустимых норм. Для этого раскисление проводят путем ввода в сталь элементов раскислителей с большим сродством к кислороду, чем железо. Образующиеся оксиды уходят в шлак. В качестве раскислителей используют кремний в виде ферросилиция, марганец (ферромарганец), алюминий и щелочно-земельные металлы.
Легирование стали осуществляют введением в расплав ферросплавов или чистых металлов в необходимом количестве. Легирующие элементы, сродство к кислороду которых меньше, чем у железа (никель, кобальт, медь, молибден и другие), при плавке и разливке практически не окисляются, и поэтому их вводят в тигель при ЭШП в любое время плавки обычно вместе со стальной шихтой. Легирующие элементы, у которых сродство к кислороду больше, чем у железа (кремний, марганец, алюминий, хром, титан и другие), вводят в металл при его раскислении или после него, а иногда непосредственно в тигель.
↑ В начало
Основные компоненты в сталях
Постоянными компонентами в углеродистых сталях являются углерод, марганец, кремний, сера, фосфор, а также скрытые компоненты в виде примесей-газов (кислорода, азота и водорода). Кроме того, в этих сталях присутствуют такие случайные компоненты, как хром, никель, медь и другие, наличие которых обусловлено загрязненностью шихтовых материалов.
↑ В начало
Полезные компоненты сталей
Полезными компонентами являются марганец и кремний, которые как правило, содержатся в шихте. Их так же вводят в сталь при ее раскислении:
FeO + Mn → Fe + Mn0
FeO + Si → 2Fe + Si02
Марганец является необходимой примесью в количестве 0,4…0,8 % при производстве различных сталей. В этих пределах он полностью растворяется в феррите и упрочняет его, увеличивает прокаливаемость стали. Марганец, устраняя вредное влияние включений оксида железа, способствует получению плотных стальных заготовок фланцев (без газовых пузырей).
В отличии от других раскислителей кремния и алюминия марганец при взаимодействия с серой
FeS + Mn → MnS + Fe
предотвращает образование сульфидов железа, повышенное содержание которых является причиной хрупкости стали, окобенно при высоких температурах.
Кремний при раскислении стали, как и марганец, устраняет вредное влияние оксида железа и способствует получению плотных заготовок фланцевых заглушек труб. Кремний повышает предел текучести стали и уменьшает ее склонность к хладоломкости. Содержание кремния в углеродистых сталях находится в пределах 0,3…0,5 %.
↑ В начало
Вредные примеси сталей
Вредными примесями в стали являются сера и фосфор.
Основным источником серы в стали является исходное сырье. Сера снижает пластичность и вязкость стали, способствует ее красноломкости при прокате и ковке. Сера образует хорошо растворимое соединение FeS (сульфид железа). Благодаря высокой ликвации серы в стали может образоваться легкоплавкая эвтектика (химическая неоднородность). При нагреве стальных заготовок до температур горячей деформации включения легкоплавкой эвтектики придают стали хрупкость, а при некоторых условиях могут плавится, и при деформировании заготовки воротникового фланца образовывать в ней трещины. Поэтому содержание серы в стали должно быть минимальным.
Фосфор является вредной примесью способной растворяться в феррите, уменьшая его пластичность. Обычно включение фосфора располагается в близи границ зерен феррита и способствует их охрупчиванию, повышая температурный порог хладоломкости.
↑ В начало
Скрытые примеси сталей
Скрытые примеси – кислород, азот и водород – находятся в стали в виде твердого раствора в феррите, или образуют химические соединения, либо присутствуют в свободном состоянии в порах металла. Повышенное содержание водорода в заготовках фланцев и заглушек труб из нержавеющих сталей (хромистых и хромоникелевых) приводят к образованию внутренних трещин – флокенов. Даже небольшие концентрации газов оказывают резко отрицательное влияние на свойства стали, ухудшая ее пластические характеристики.
↑ В начало
Влияние легирующих элементов на свойства фланцев из нержавеющей стали. Фланцевые заглушки, стальные переходы, коррозионно-стойкие стали.
Легирующими элементами называют специальные добавки, вводимые в сталь для изменения ее строения и свойств. Стали, содержащие легирующие элементы, называются легированными. Легирование стали изменяет ее:
- механические свойства (прочность, пластичность, вязкость),
- физические (электропроводность, магнитные характеристики, радиационная стойкость) и
- химические свойства (коррозионная стойкость в разных средах).
Концентрация некоторых легирующих элементов может быть очень малой. Легирование стали, когда концентрация вводимого элемента составляет 0,1% и менее, называют микролегированием.
Основными легирующими элементами являются Mn, Si, Cr, Ni, W, Mo, Co, Ti, V, Zr, Nb и другие. Легирующие элементы по разному влияют на свойства стали.
Марганец повышает прочность, износостойкость, а так же глубину прокаливаемости стали при термической обработке.
Кремний способствует получению более однородной структуры, улучшает упругие характеристики стали, повышает магнитные свойства стали, предает ей кислотоупорность.
Хром повышает твердость, прочность, а при термической обработке увеличивает глубину прокаливаемости стали, оказывает положительное влияние на жаропрочность и жаростойкость, повышает коррозионную стойкость стали (фланцы жаропрочные 15Х5М, нержавеющие фланцы и заглушки труб, стальные концентрические и эксцентрические переходы).
Никель действует так же как и марганец. Кроме того, он повышает электросопротивление стали и снижает значение коэффициента линейного расширения (фланцы сосудов и аппаратов из "нержавейки").
Вольфрам уменьшает величину зерна, повышает твердость и прочность, улучшает режущие свойства стали при повышенной температуре (фланцы 12Х18Н10Т).
Молибден действует, как и вольфрам, а так же повышает коррозионную стойкость стали (фланцы нержавеющие, фланцы молибденовые сталь 10Х17Н13М2Т).
↑ В начало
Контроль плавки кольцевых заготовок фланцев и заглушек труб. Механические свойства. Литые фланцы. Качество деталей трубопроводов.
Контроль плавки при производстве стали ведется по пробам металла, которые берут специальной металлической ложкой. Прежде чем опустить ложку в металл, ее покрывают слоем шлака для того, чтобы она не расплавилась. После этого зачерпывают металл и выливают его в маленькую форму или на металлическую плиту. При сливе жидкой стали на плиту можно сделать заключение о температуре разогрева металла. Горячий металл легко растекается по плите и приваривается к ней. Более точные данные о температуре металла получают при измерении температуры при помощи термопар или оптических пирометров.
Пробу, залитую в форму, подвергают химическому или спектральному анализу в экспресс-лаборатории. В течение плавки пробы берут до тех пор, пока не получаем металл заданного состава.
Для проверки степени раскисленности металла берут технологическую пробу, для чего отливают образец и куют его в горячем состоянии. Не раскисленный металл содержит FeO, и при ковке образец дает трещины. Раскисленный металл при ковке не разрушается и не имеет трещин. Он пластичен.
Механические испытания проводят на стандартных образцах. Если необходимо, определяют макро- и микроструктуру стали. Кроме проб металла, берут пробы шлака. Пробы необходимы для определения его жидкотекучести, цвета и в отдельных случаях – химического состава.
Присутствующие в стали неметаллические включения и газы резко снижают ее прочностные и эксплуатационные характеристики. В связи с этим разработано большое количество способов очистки стали. На предприятии ООО "Инженерный Союз" используется электрошлаковый переплав.
↑ В начало
Электрошлаковый переплав как способ повышения качества стали фланцев.
Детали трубопроводов и фланцы высокого давления, больших диаметров.
Способ электрошлакового переплава (ЭШП) расходуемых электродов в кристаллизаторе или тигле нашел широкое применение для получения коррозионно-стойких и других сталей специального назначения. Переплаву подвергается сортовой металл или порезанный на круглые прутки металл, сваренный в расходуемый электрод. Электрошлаковый переплав считается наиболее эффективным методом рафинирования, так как после него содержание серы в металле снижается почти в два раза, уменьшается количество оксидов, неметаллических включений и растворенных газов.
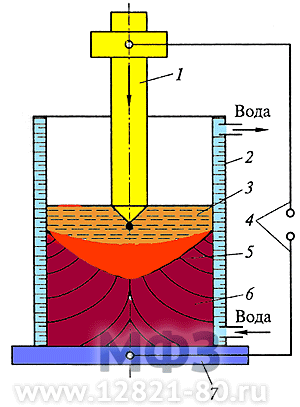
Рис. 1. Схема установки электрошлакового переплава:
1 – электрод; 2 – кристаллизатор; 3 – шлак;
4 – токоподводящие кабели; 5 – ванна;
6 – слиток; 7 – поддон.
Схема установки электрошлакового переплава приведена на рисунке 1. Между электродом 1 из переплавляемой стали и наплавляемым слитком 6 находится слой электропроводящего шлака 3, который предварительно плавят и заливают в кристаллизатор 2. В состав шлака входят Al2O3, CaO и CaF2.
При прохождении электрического тока через шлак выделяется теплота, нагревающая его до температуры 1700°C. Металл расходуемого электрода плавится, каплями стекает сквозь слой шлака и образует металлическую ванну 5, расположенную на поддоне 7. Такой способ обеспечивает большую площадь соприкосновения металла со шлаком и усиливает протекание процессов рафинирования стали.
Под слоем шлака в кристаллизаторе (тигле) постепенно наплавляется слиток. Направленная кристаллизация металла способствует получению плотного однородного расплава или слитка. Слитки выплавляют круглого, и прямоугольного сечения с массой до нескольких тонн.
↑ В начало
Центробежное литье кольцевых заготовок воротниковых фланцев
Заглушки фланцевые труб, стальные переходы, прокладки
Центробежное литье – способ изготовления отливок (заготовки фланцев, заготовки заглушек, труб, концентрические переходы и другие детали вращения), при котором заполнение формы расплавом и его затвердевание происходит в поле действия центробежных сил.
Схемы получения отливок деталей трубопроводов центробежным литьем при вращении формы показаны на рисунке 2.
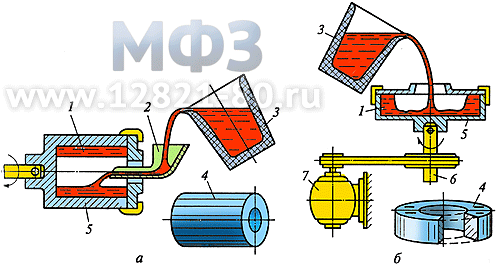
Рис. 2. Схема изготовления отливок центробежным литьем
при вращении формы:
а – вокруг горизонтальной оси; б – вокруг вертикальной оси;
1 – расплав; 2 – желоб; 3 – ковш; 4 – отливка (литая заготовка);
5 – форма; 6 – шпиндель; 7 – электродвигатель.
Наиболее часто используют два варианта, при которых расплав заливается в форму: 1) с горизонтальной и 2) с вертикальной осями вращения. В первом случае получают отливки в виде тел вращения различной длины, во втором – отливки в виде тел вращения малой длины и фасонные (фланцы юбочные, или воротниковые, или фланцы стальные приварные встык). Формы приводятся во вращение машинами, называемыми центробежными.
Наиболее распространен способ литья во вращающиеся металлические формы с горизонтальной осью вращения (рис. 2, а). При этом способе отливка формируется в поле центробежных сил и имеет свободную поверхность, не соприкасающуюся с поверхностью формы.
Формообразующей для отливки служит внутренняя поверхность формы (изложница). Расплав из ковша 3 заливают во вращающуюся форму 5 через заливочный желоб 2. Расплав 1 растекается по внутренней поверхности формы и под действием центробежных сил образует пустотелый цилиндр. После затвердевания металла отливка 4 извлекается из формы.
Однако на производстве ООО "Инженерный Союз" с учетом специфики производимых деталей трубопроводов наиболее широко применяется получение отливок в форме с вертикальной осью вращения (рис. 2, б): расплав из ковша 3 заливается в форму 5, укрепленную на шпинделе 6, приводимом во вращение от электродвигателя 7. В процессе вращения формы 5 расплав 1 под действием центробежных сил отбрасывается к ее стенкам и затвердевает.
После затвердевания расплава машину останавливают и извлекают кольцевую заготовку.
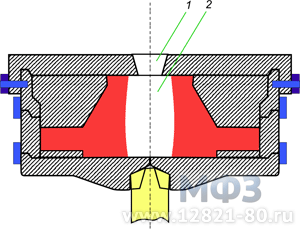
Рис. 3. Схема изготовления фасонных литых
заготовок воротниковых фланцев
(фланцев стальных приварных встык):
1 – стояк; 2 – центральная полость формы.
При центробежном литье обычно используют металлические формы, которые предварительно подогревают, после чего на рабочую поверхность формы наносят покрытие. Применение покрытия повышают стойкость форм, снижает скорость охлаждения отливок, уменьшает вероятность образование в отливках спаев и трещин.
Скорость вращения формы оказывает большое влияние на затвердевание и охлаждение отливки. При неправильном выборе скорости в формируемой отливке (фланцевая заглушка труб) могут появиться специфические дефекты – спаи, трещины и ликвация (химическая неоднородность).
Существуют различные формулы для расчета частоты вращения изложницы n (мин-1). Например, для литья на машинах с горизонтальной осью вращения частоту определяют по формуле
,
где ρ – плотность сплава отливки, кг/м3; r – внутренний радиус отливки, м.
Центробежное литье обеспечивает получение плотных отливок и облегчает выход на свободную поверхность шлаковых и газовых включений. Перемешивание металла в процессе литья препятствует направленному росту кристаллов, что способствует образованию в отливке мелкой и плотной структуры.
↑ В начало
Заключение
При изготовлении деталей трубопроводов необходимо учитывать все многообразие физико-химических и механических характеристик поведения металлов и их сплавов в тех или иных условиях изготовления и эксплуатации, ведь малые колебания концентрации того или иного элемента могут значительно изменить микро- и макроскопические характеристики материала детали.
В заключение стоит отметить, что описанная выше технология переплава и литья успешно применяется в современном производстве деталей трубопроводов ответственного назначения.
↑ В начало
Список литературы
- Гини Э. Ч. Технология литейного производства : Специальные виды литья / Э. Ч. Гини, А. М. Зарубин, В. А. Рыбкин ; под ред. В. А. Рыбкина – М. : Изд. центр «Академия», 2006.
- Специальные способы литья : справочник / под ред. В. А. Ефимова.. – М. : Машиностроение, 1991.
- Титов Н. Д. Технология литейного производства / Н. Д. Титов, Ю. А. Степанов.. – М.: Машиностроение, 1985.
Получив доступ к данной странице, Вы автоматически принимаете Пользовательское соглашение.