Мелкоотходные заготовки фланцев: полунепрерывно- и непрерывнолитые, заготовки из сортового проката
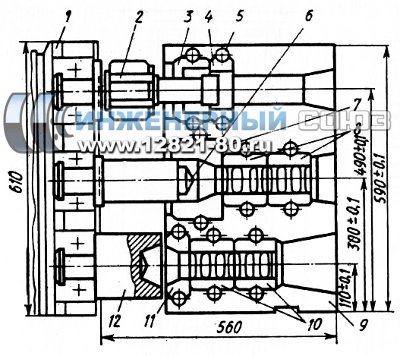
Высадочный штамп для поковки кольцевой заготовки фланца
Исходными стальными заготовками для ковки и объемной штамповки заготовок фланцев служат слитки и сортовой прокат. Применение научных исследований и новых технологических разработок в процессе производства заготовок для деталей трубопроводов позволяет значительно снизить затраты энергии и сырья, а также заметно повышает качество готовых элементов трубопроводов.
Дата публикации: 21 января 2011
Содержание
Для ковки и горячей объемной штамповки фланцевых заготовок применяют углеродистые, легированные и высоколегированные стали, а также жаропрочные, титановые, алюминиевые, магниевые, медные, хром-никелевые и другие сплавы. Исходными стальными заготовками для ковки и объемной штамповки фланцев служат 1) слитки и 2) сортовой прокат.
Слитки для фланцевых заготовок
Основной вид исходной заготовки для производства крупных поковок, заготовок фланцев (в том числе уникальных, широко используемых в современном тяжелом, транспортном, химическом и энергохимическом машиностроении), изготавливаемых на гидравлических прессах, – слиток. В связи с тенденцией увеличения мощности машин и механизмов, увеличением давления и пропускной способности продуктопроводов, особенно агрегатов энергетического машиностроения, нефтехимических и газовых трубопроводов, потребность в производстве крупных слитков растет.
По размерам и конфигурации кузнечные слитки выплавляются в соответствии с различными ведомственными нормалями и техническими условиями массой до 300 тонн. В 1984 г. ПО «Ижорские заводы» был отлит самый крупный в стране уникальный слиток массой 360 тонн, а в 1988 г. на заводе отлили слиток-гигант массой 420 тонн. На очереди отливка слитков массой 450 и 500 тонн. Крупный слиток массой 570 тонн отлит в Японии. В наши дни у России существует возможность отливать ещё более массивные кузнечные слитки: в сталеплавильный комплекс ДСП-120 Ижорских заводов входит дуговая печь, позволяющая отливать уникальные кузнечные слитки массой до 600 тонн. Из кузнечных слитков машиностроительные предприятия России ежегодно производят более 2 млн. тонн поковок. Технологические возможности плавильных установок завода ООО «Инженерный Союз» позволяют изготавливать литые кольцевые заготовки фланцев массой до 3 тонн.
Отходы при производстве слитков
Отношение высоты слитка Н, используемые при производстве поковок, к среднему D обычно не превышает 2,5. При изготовлении поковок и слитков отходы донной части слитка составляют 5,8%, отходы прибыльной части 18,22%, а у слитков из легированной стали в отдельных случаев достигает 30% и более. Поэтому перед металлургами стоит важнейшая задача – разработать и освоить технологию выплавки высококачественных малоотходных слитков.
Модернизация слитков
В последние годы кузнечный слиток, как исходная заготовка для ковки, претерпевает значительные изменения. Форма слитка совершенствуется, изменяется его конфигурация и внутреннее строение применительно к определенному виду поковок, например заготовки фланцев, заготовки концентрических переходов, заготовки фланцевых заглушек, заготовки тройников бесшовных, заготовки стальных прокладок.
В цехах ООО «Инженерный Союз» освоено производство различных типов заготовок соединительных деталей трубопроводов, экономичных кузнечных слитков: удлиненных, малоприбыльных и бесприбыльных, обеспечивающих снижение расхода металла и значительное повышение выхода годного изделия при производстве поковок.
В последние годы при изготовлении поковок широко используют удлиненные слитки, которые впервые были разработаны и освоено их производство в советский период . Удлиненные слитки отливают с соотношением H/D = 3,3…4,5. Прибыльная часть имеет такую же форму, как и слиток. Отходы прибыльной части составляют всего около 12%, а донной части – 3%. По сравнению с обычными слитками такой же массы, удлиненные слитки характеризуются повышенной плотностью и однородностью металла. В настоящее время широко применяют удлиненные слитки массой до 13 тонн.
Замена обычных слитков удлиненными весьма эффективна. Трудоемкость термомеханической обработки, отходы металла прибыльной и донной частей сокращаются, что увеличивает выход годных изделий в кузнечно-прессовых цехах. Экономичность применения удлиненных слитков по сравнению с обычными показана в Таблице.
Экономичность применения удлиненных слитков
Масса слитка, т | Выход годного, % | Продолжительность нагрева перед плавкой, ч | Экономия от применения удлинённых слитков, % | |
топлива | машинного времени | |||
3,8 / 2,95 | 59,8 / 77,0 | 12,0 / 5,5 | 54 | 31 |
4,2 / 3,5 | 64,0 / 77,0 | 12,0 / 5,5 | 54 | 25 |
7,3 / 5,8 | 61,0 / 77,0 | 17,5 / 7,0 | 60 | 35 |
12,0 / 10,5 | 63,2 / 77,0 | 19,3 / 13,0 | 68 | 37 |
Примечание: цифры в числителе относятся к обычным слиткам, а в знаменателе – к удлиненным слиткам.
Анализ приведенных в этой таблице данных показывает, что внедрение в производство удлиненных слитков при ковке одних и тех же поковок повышает выход годного до 77% ,вместо 59,8–64%, снижает расход топлива на 54–68% за счет уменьшения сечения слитков и числа нагревов, увеличивает производительность ковочных прессов за счет сокращения машинного времени на 25–37%, уменьшает продолжительность нагрева перед ковкой на 31–54%.
↑ В начало
Непрерывнолитые заготовки
В последние годы широко распространены малоотходные технологии ковки поковок из малоприбыльных (как обычных, так и удлиненных) и бесприбыльных слитков. Бесприбыльные слитки получают наполнением изложниц до заданного уровня с контролем массы залитого металла на электронных весах. Применяют малоприбыльные слитки с объемом прибыли 70 и 40% от номинального при ковке заготовок типа втулок, колец, цилиндров, деталей вращения и других пустотелых поковок, получаемых осадкой с последующей прошивкой и протяжкой на оправке под молотом или прессом. Металл усадочной раковины и другой дефектный металл, располагаемый возле нее, удаляется при прошивке в выдру. Использование малоприбыльных и бесприбыльных слитков дает возможность повысить выход годного изделия на 5–10%.
Для ковки крупных поковок типа колец, бандажей, цилиндров, обечаек и других наиболее рациональными исходными заготовками служат полые слитки массой до 140 тонн, применение которых позволяет экономить 25–30% металла за счет отсутствия выдры, уменьшения массы прибыли, поддона и угара при сокращенном числе нагревов. Кроме того, цикл ковки сокращается в 2,3 раза, так как при этом исключаются трудоемкие операции оттяжки под патрон, биллетировка, осадка и прошивка заготовки, которые неизбежны при ковке сплошного слитка.
Радикальным методом снижения потерь металла при изготовления исходных заготовок для кузнечно-штамповочного производства служит получение их непрерывным или полуненпрерывным литьем. Поскольку ковка на прессах и молотах носит единичный и мелкосерийный характер, то совместная работа машин непрерывного литья заготовок и кузнечно-прессового оборудования затруднена. Поэтому целесообразно в сталелитейных цехах заводов применять не непрерывный, а полунепрерывный процесс литья заготовок, который в большей степени соответствует характеру кузнечно-прессового производства. Исследование показывают, что использование в машиностроении непрерывнолитых заготовок в замен проката позволяет уменьшить отходы металла в среднем на 25%. Снижение себестоимости деталей, производимых из непрерывнолитых заготовок составляет 15%. Из непрерывно литых заготовок можно изготавливать до 70% поковок, получаемых из проката.
При непрерывной разливке сокращается не только расход металла, но и затраты топлива. Однако таким методом производится лишь незначительная часть стали, тогда как в зарубежных странах им получают гораздо больше стали.
Для отливки кузнечных заготовок из углеродистых, легированных и высоколегированных марок стали используют машины полунепрерывного литья заготовок.
↑ В начало
Сортовой прокат для изготовления заготовок фланцев
Исходными заготовками при ковке на молотах и горячей объемной штамповке на различном штамповочном оборудовании служит прокат из черных и цветных металлов, а также различный нержавеющий прокат, которые поставляют согласно стандарту на сортамент круглого и стандартного сечений. Круглый прокат поставляют диаметром от 5 до 250 мм, квадратный (со стороной квадрата от 5 до 250 мм) длиной от 2 до 12 метров.
В значительной степени экономия металла зависит от качественных характеристик катаных заготовок. Повышение качества проката дает возможность сэкономить по нашим оценкам до 25 млн. тонн металла в год, а тонна проката повышенной точности позволяет сократить расход металла на 0,3–0,5 тонны; низколегированного и упрочненного проката – на 0,2–0,3 тонны. Кроме того, применение высококачественного металла для изготовления деталей машин, ответственных узлов, трубопроводов дает реальную возможность продлить сроки службы оборудования на 30%.
Крупным резервом экономии металла в нефтехимическом машиностроении является применение экономичных профилей проката – профильного и периодического проката. Норма расхода металла на изделие при применении периодического проката вместо сортового проката черных металлов уменьшается в среднем на 10–30%, трудоемкость обработки на 20–40%, а его использование при горячей штамповке значительно снижает потери металла в облой. Например, при производстве воротниковых фланцев горячей штамповкой коэффициент использования металла (КИМ) повышается на 10–15%. Применение профильного проката для штамповки поковок в открытых штампах и трубных заготовок для штамповки выдавливания пустотелых поковок и раскатки позволяет снизить потери металла при разрезке труб, и в 2–3 раза повысить КИМ. При этом трудоемкость изготовления поковок уменьшается на 20–50%. На нашем кузнечном производстве изготовление заготовок фланцев методом горячей штамповки позволяет получать объективную себестоимость годной продукции (фланцы воротниковые, фланцы сосудов и аппаратов, и другие детали трубопроводов).
↑ В начало
Заключение
Применение научных исследований и новых технологических разработок в процессе производства заготовок для деталей трубопроводов позволяет значительно снизить затраты энергии и сырья, а также заметно повышает качество готовых элементов трубопроводов.
Список литературы
- Брюханов А.Н. Ковка и объёмная штамповка.. – М.: Машиностроение, 1975. – 408 c.
- Кузьминцев В.Н. Ковка на молотах и прессах.. – М.: Высшая школа, 1979. – 256 c.
- Охрименко Я.М Технология кузнечно-штамповочного производства : Учебник для вузов.. – М.: Машиностроение, 1976. – 560 c.
Получив доступ к данной странице, Вы автоматически принимаете Пользовательское соглашение.