Поточная линия производства фланцев середины прошлого века
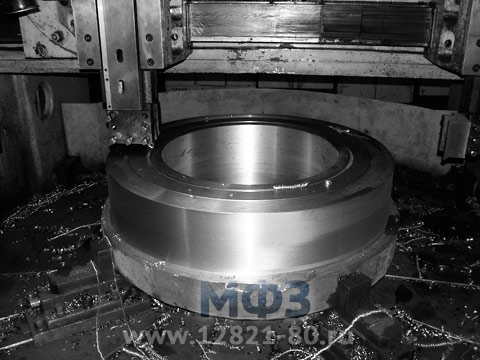
Обработка фланца на токарно-карусельном станке
Описание проекта поточной линии производства фланцев, заглушек и колец, внедрённого в начале 1960-х годов. Токарный станок для расточки внутренних отверстий деталей трубопроводов, оптимизация промышленного оборудования под производственные задачи.
Дата публикации: 13 января 2011
Поточная линия производства деталей трубопроводов
Эта статья продолжает обсуждение производства фланцев полувековой давности, где мы рассматривали первый этап производства – организацию заготовительного цеха по производству заготовок деталей трубопроводов.
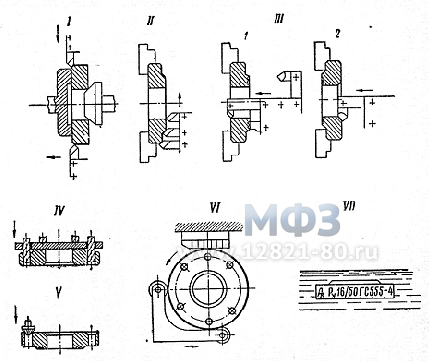
Рис. 1. Схема технологического процесса
обработки фланцев. Последовательность
операций обозначена римскими цифрами.
Далее в на производственной линии следуют (рис. 1):
- операция II (рассматриваться здесь не будет) – подрезка наружного ступенчатого конца, снятие фаски нужного диаметра;
- операция III – расточка центрального отверстия фланца или кольца, снятие фаски на кромке внутреннего диаметра;
- операция IV – сверление отверстий под фланцевый крепеж;
- операция V – зенкование крепежных отверстий для шпилек и болтов.
Здесь подробно будет рассматриваться токарный станок для обработки внутреннего диаметра деталей трубопроводов (фланцев, заглушек фланцевых и приварных колец для свободных фланцев) в составе поточной производственной линии.
Инженерное проектирование на основе метода поточной групповой обработки
Рассматриваемая нами поточная линия спроектирована на основе метода групповой обработки деталей, при котором каждый станок модернизирован и оптимизирован применительно к групповому техническому процессу, т. е. оснащен только теми средствами автоматизации и механизации и только такими приспособлениями, которые необходимы для высокопроизводительной обработки деталей данной группы.
Главными направлениями модернизации оборудования при групповом методе обработки деталей являются:
- увеличение быстроходности и мощности станков;
- изменение технологических возможностей станков в соответствии с особенностями группового технологического процесса;
- сокращение вспомогательного времени путем механизации отдельных приемов работы на станках и применения быстродействующих приспособлений;
- автоматизация цикла работы станков;
- сокращение подготовительно-заключительного времени за счет применения средств и методов быстрой настройки станков.
При внедрении группового метода получения трубопроводной продукции в серийное производство открываются возможности не только для широкого использования специализированных и агрегатных станков, обеспечивающих высокую производительность, но и для создания групповых механизированных многопредметных поточных линий.
Поточный метод производства является наиболее прогрессивной и экономически выгодной формой организации производственного процесса. Поточный процесс при любой форме потока характеризуется высокой производительностью, использованием передовой технологии, совершенной организацией производства, а также строгой синхронизацией отдельных операций, обеспечивающей ритмичность выпуска продукции.
Приспособления, применяющиеся на поточной линии, являются групповыми; с их помощью можно обрабатывать все детали группы или значительную часть этих деталей.
На токарных станках применяются оправки и патроны со сменными зажимными элементами, дающими возможность обрабатывать все типы фланцев и колец, входящих в группу. На многошпиндельных сверлильных станках используются сменные кондукторные плиты, позволяющие обрабатывать до десяти типоразмеров деталей; установочные приспособления на этих станках обеспечивают обработку всей группы деталей с незначительной переналадкой и т. д.
Разбивка группы деталей на подгруппы стальных фланцев и колец различных типов, но имеющих одинаковые основные размеры, позволила в 3—4 раза снизить количество наладок и производить только несложную подналадку оборудования, которая занимает несколько минут и которую в состоянии выполнить сам станочник, в то время как наладка производится наладчиком линии.
Токарный станок для расточки внутренних отверстий фланцев и колец
На токарно-винторезном станке 1Д62М, специализированном для выполнения III по счёту технологической операции, при первой установке растачивается отверстие и прорезаются уплотнительные канавки, а при второй — снимается фаска на кромке внутреннего диаметра детали. Станок оснащен такими механизмами и устройствами, которые позволяют механизировать и в значительной степени автоматизировать цикл обработки деталей. К ним относятся:
- механизм ускоренного перемещения продольного суппорта и
- пневматический трехкулачковый патрон, аналогичные рассмотренным выше, а также
- модернизированные коробки скоростей и подач.
Для автоматического отключения продольной подачи предназначен микропереключатель, замыкающий цепь электромагнита, смонтированного на фартуке. Сердечник электромагнита шарнирно соединен с рычагом, установленным вместо рукоятки отключения падающего червяка.
Так же как и на токарном станке, специализированном для выполнения II операции, на фартуке описываемого станка расположен конечный выключатель, управляемый кулачком, закрепленным на рычаге.
Цикл обработки детали состоит из следующих операций:
- деталь закрепляется в кулачках пневматического патрона;
- затем поворотом рычага, установленного на валике включения падающего червяка, включаются электродвигатель станка и продольная подача суппорта;
- после окончания растачивания отверстия микропереключатель входит в соприкосновение с жестким упором, закрепленным на станке;
- цепь катушки электромагнита замыкается, и
- сердечник, втягиваясь, поворачивает рычаг, в результате чего происходит отключение продольной подачи, быстрый отвод суппорта и отключение электродвигателя станка.
Автоматическое отключение продольной подачи микропереключателем позволило повысить точность получения требуемых размеров фланцев.
Фаски на кромке внутреннего диаметра фланцев особых типов снимаются со второй установки детали, при этом головка резцедержателя поворачивается и с помощью рычага снова включаются электродвигатель станка и продольная подача суппорта.
Наладка станка заключается в установке оправок с резцами, позволяющими совместить растачивание отверстия с прорезанием уплотнительных канавок, а также в установке резца для снятия фаски и регулировании жесткого упора, расположенного на станине станка.
Заключение
Таким образом, применение метода групповой обработки деталей на основе отыскания их сходных свойств и классификации по различным признакам приводит к увеличению качества и скорости производства, а также к снижению стоимости деталей трубопроводов.
Список литературы
- Кучер И. М., Кучер А. М. Модернизация и автоматизация станков.. – М. : Машгиз, 1958.
- Митрофанов С. П. Научные основы групповой технологии.. – Л. : Лениздат, 1959.
Получив доступ к данной странице, Вы автоматически принимаете Пользовательское соглашение.