Технологии производства фланцев и крепёжных изделий горячей обработкой металлов давлением
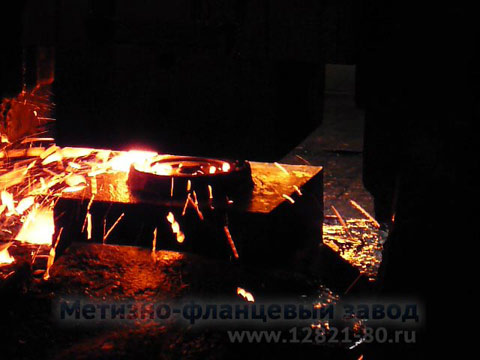
Штамповка заготовки фланца
Обработка металлов давлением основана на способности металлической заготовки пластически деформироваться, то есть изменять форму и размеры в результате приложения внешней силы. Основными видами такой обработки являются прокатка, прессование, волочение, ковка, объёмная штамповка, листовая штамповка. Объёмную штамповку обычно применяют в серийном и массовом производстве деталей трубопроводов, где особенно необходимы высокая производительность и большая точность поковок.
Дата публикации: 3 декабря 2010
Содержание
1. Понятие о горячей обработке металлов давлением
2. Виды горячей обработки металлов давлением
2.7. Получение деталей, не требующих обработки
2.8. Физические процессы, происходящие при ковке и объёмной штамповке фланцев и фланцевого крепежа
3. Сравнительная экономическая характеристика ковки и объёмной штамповки фланцев и крепежных изделий
Понятие о горячей обработке металлов давлением
Обработка металлов давлением основана на способности металлической заготовки пластически деформироваться, то есть изменять форму и размеры в результате приложения внешней силы. Пластическая деформация, в отличие от упругой, является необратимой, то есть после снятия нагрузки форма и размеры заготовки не восстанавливаются.
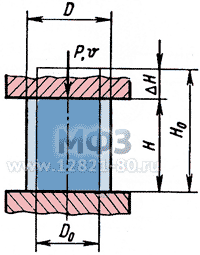
Рис. 1. Схема деформации цилиндрической
заготовки при её осадке в идеальных условиях
(без учёта сил трения)
Различают деформацию абсолютную, то есть абсолютное изменение какого-либо геометрического параметра деформируемого тела, и относительную, определяемую как отношение абсолютного изменения этого параметра к его первоначальному значению. При осадке цилиндрической заготовки её начальная высота Н0 уменьшается до конечной высоты Н; в этом случае значение абсолютной деформации ΔН= Н0– Н; степень деформации (сжатие) всей заготовки характеризуется относительной деформацией ε= ΔН/Н0.
Абсолютная деформация заготовки осуществляется с определенной скоростью, называемой скоростью деформирования Hv= ΔН/τ, где τ – время деформации. Скорость деформирования следует отличать от скорости деформации, под которой понимают изменение относительной деформации в единицу времени. На участке ΔН средняя скорость деформации εv = ε/τ. Единицей скорости деформации является с-1. При осадке заготовки с постоянной скоростью деформирования скорость деформации непрерывно увеличивается, поскольку за одно и то же время возрастает относительная деформация (обратная картина наблюдается при растяжении). Допустимая степень деформации металлической заготовки при ее обработки давлением определяется пластичностью металла и его сопротивлением деформированию. Пластичность – свойство металла деформироваться без разрушения. Количественно пластичность оценивают при испытании образца на растяжение, сжатие и кручение по значению предельной относительной деформации, соответствующей появлению первых признаков разрушения. Пластическая деформация заготовки начинается и заканчивается при определенных напряжениях, возникающих под действием внешней силы и характеризующих такое свойство металла, как сопротивление деформированию.
При пластической деформации в металле одновременно протекают процессы двух видов – упрочняющие (повышающие напряжение течение металла), зависящие в основном от относительной деформации, и разупрочняющие, зависящие от температуры и времени деформации. Увеличение скорости деформации приводит к уменьшению времени протекания разупрочняющих процессов, в результате чего возрастает сопротивление металла деформированию. При этом пластичность металла, как правило, снижается. Наибольшее влияние на интенсивность протекания разупрочняющих процессов в металле оказывает температура его нагрева. При нагреве металлов пластичность резко повышается, а сопротивление деформированию снижается, поэтому большинство металлов и сплавов подвергают горячей обработке давлением (исходную заготовку нагревают специальным устройством, а затем обрабатывают на деформирующей машине). Исключения составляют свинец, медь, низкоуглеродистые стали и другие, которые достаточно пластичны в холодном состоянии и могут обрабатываться без нагрева.
↑ В начало
Виды горячей обработки металлов давлением
Основными видами такой обработки являются прокатка, прессование, волочение, ковка, объёмная штамповка, листовая штамповка.
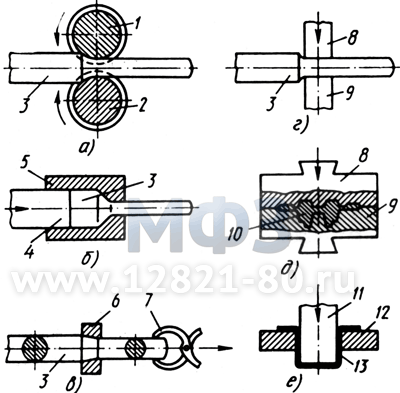
Рис. 2- Схемы горячей обработки заготовки давлением при продольной
прокатке (а), прессовании (б), волочении (в), ковке (г), объёмной (д)
и листовой (е) штамповке: 1, 2 – валки, 3 – заготовка, 4, 11 – пуансоны,
5, 12 – матрицы, 6 – волока, 7 – клещи,
8, 9 – подвижный и неподвижный бойки, 10 – полость, 13 – изделие.
↑ В начало
Прокатка
Прокатка осуществляется путём обжатия заготовки между вращающимися волками. Различают продольную, поперечную и поперечно-винтовую прокатку. При продольной прокатке (рис. 2, а) валки 1 и 2 вращаются в разные стороны, при этом толщина заготовки 3 уменьшается, а длина увеличивается. Для прокатки листов применяют валки с гладкой поверхностью, а для прокатки сортовых профилей (прутков круглого и квадратного сечений, прутков шестигранного сечения, для изготовления заготовок и производства гаек, болтов), балок, швеллеров, рельсов – фасонные.
Машины, на которых осуществляют прокатку, называют прокатными станами. На прокатных станах из стальных слитков получают блюмы (крупные заготовки квадратного или прямоугольного сечения) и слябы (заготовки с обжатыми боковыми кромками). Блюмы являются полуфабрикатом для последующей прокатки профилей постоянного и переменного по длине сечения, а так же заготовками для ковки, слябы – полуфабрикатом для прокатки листа. Заготовки с периодически повторяющимися по длине сечениями, получаемые продольной или поперечно-винтовой прокаткой, называют периодическим прокатом. Его используют в качестве полуфабриката для последующей штамповки деталей с вытянутой осью, например балки, оси, валы.
Разновидностью продольной прокатки является вальцовка, которую выполняют на ковочных вальцах. Вальцовку обычно применяют с целью получения фасонных заготовок для последующей штамповки (формовочная вальцовка) и реже – для получения вальцовых поковок (штамповочная вальцовка). Разновидностью поперечной прокатки является поперечно-кленовая прокатка, с помощью которой в кузнечных цехах объёмной штамповки получают валики, сверла и другой инструмент.
↑ В начало
Прессование
Прессование(рис. 2, б) заключается в выдавливании металла заготовки 3 из контейнера в отверстие матрицы 5 под действием пуансона 4. В результате сечение заготовки уменьшается, а длина, соответственно, увеличивается. Поперечное сечение прессованного изделия имеет форму отверстия матрицы; оставшийся в контейнере металл (пресс-остаток), являющийся технологическим отходом, отрезают. Прессование, как правило, осуществляют на гидравлических прессах, изготовляя прутки и профили сложной формы. Процесс получения изделия типа болты, чаще головку болта формируют высадкой, ковкой. Процесс получения изделия типа стержня с головкой, когда остающийся в контейнере металл является частью изделия, называют выдавливанием. Этот способ широко применяют, например, для изготовления клапанов двигателей внутреннего сгорания. Наиболее распространенным оборудованием для выдавливания являются вертикальные гидравлические или механические прессы.
↑ В начало
Волочение
Волочение (рис. 2, в) заключается в протягивании ранее катанной или прессованной заготовки 3 через отверстие (фильеру) волоки 6, в результате чего поперечное сечение изделий несколько уменьшается. Этот вид обработки применят для повышения точности и улучшения поверхности изделия и осуществляют на волочильных станках. Заострённый конец заготовки захватывают клещами 7, к которым прикладывают тянущее усилие. Клещи установлены в каретке, приводимой в движение от электродвигателя через цепную передачу.
↑ В начало
Ковка
Ковка (рис. 2, г) – это процесс обработки заготовки 3 подвижным бойком 8 на неподвижном 9. Металл свободно течет в направлениях, неограниченных поверхностью инструмента. Различают ручную ковку, когда кузнец ударяет кувалдой по нагретой заготовке, помещенной на наковальню, и машинную, при которой бойки закреплены в рабочем пространстве деформирующей машины молота или пресса. На нашем кузнечном производстве свободной машинной ковкой изготавливается незначительное количество заготовок фланцев.
↑ В начало
Объёмная штамповка
Объёмная штамповка (рис. 2, д) отличается от ковки тем, что бойки 8 и 9 имеют полость 10 (ручей, гравюру), соответствующую конфигурации изделия, например воротниковый фланец. При штамповке течение металла в сторону ограничено поверхностью инструмента, поэтому при смыкании половин штампа (бойков) металл заполняет ручей. Заготовка воротниковых фланцев, выполненная объёмной штамповкой, превалирует в заготовительном производстве фланцев и других деталей трубопроводов.
↑ В начало
Листовая штамповка
Листовая штамповка (рис. 1.2, е) – изготовление изделия 13 из листового металла с помощью штампа (пуансона 11 и матрицы 12). Этот вид горячей обработки применяют обычно для получения изделий из толстолистовых или низкопластичных металлических заготовок и осуществляют на листоштамповочных прессах. Наше метизное производство успешно изготавливает таким методом плоские шайбы, иногда – квадратные. Квадратные шайбы из листового нержавеющего проката по экономическим расчетам (снижение себестоимости) также выполняются рубкой на гильотинах.
↑ В начало
Получение деталей, не требующих обработки
Прокатку, прессование, волочение широко применяют в металлургическом производстве. Получаемые изделия могут использоваться в готовом виде без дальнейшей обработки (трубы, профили), а так же служить полуфабрикатом для других деталей, получаемых в процессе последующей обработки в кузнечных и листоштамповочных цехах. Изготовление деталей трубопровода, а именно, переходов концентрических и эксцентрических невысокого давления и малых условных диаметров происходит по указанной технологии. И всё-таки основу кузнечно-штамповочного производства составляет ковка и объёмная штамповка.
↑ В начало
Физические процессы, происходящие при ковке и объёмной штамповке фланцев и фланцевого крепежа
Что же происходит с металлом в процессе ковки и штамповки? Опишем эти процессы математически. При ковке и объёмной штамповке деформирующие усилия передаются заготовке через поверхность её контакта с подвижным инструментом. Среднее удельное усилие можно определить как отношение полного усилия деформирования к площади контакта, например, при осадке (см. рис. 1)
р=Р/F, где р – среднее удельное усилие в данный момент деформации (при относительной деформации ε= ΔН/Н0; Р – усилие осадки; F – текущая площадь контакта с инструментом. Площадь F определяют из условия постоянства объёма, согласно которому объём тела до пластической деформации равен его объёму после деформации, то есть
F= V/H,
где V - объём заготовки
V= π*D20H0/4
Удельное усилие практически всегда можно выразить как p = kσT, где σT – напряжение, учитывающее природу обрабатываемого металла и температуру деформации (предел текучести, значение которого выбирается по справочным данным; при горячей деформации вместо предела текучести в расчетах часто используется предел прочности); k – безразмерный коэффициент, учитывающий схему процесса деформации, скорость деформации, трение на поверхности контакта, а так же масштабный фактор, отражающий неодинаковую степень остывания нагретых заготовок различных размеров.
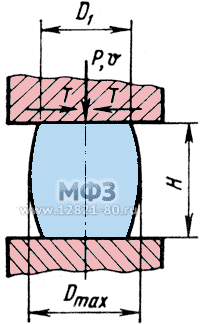
Рис. 3. Схема осадки цилиндрической заготовки
при действии сил трения.
Трение на поверхности контакта между заготовкой и инструментом затрудняет течение поверхностных слоев заготовки, увеличивает неоднородность деформации, приводит к возрастанию удельного и полного усилий деформирования. При осадке в результате действия сил трения Т (рис. 3) цилиндрическая заготовка приобретает бочкообразность, а действительная площадь контакта F1 оказывается меньше площади F, так как D1
↑ В начало
Сравнительная экономическая характеристика ковки и объёмной штамповки фланцев и крепежных изделий
Изделия, получаемые в результате ковки или объёмной штамповки, называют поковкой. Поковку для одной и той же детали (фланцы плоские или воротниковые, фланцы сосудов и аппаратов, заглушки фланцевые, поворотные заглушки) можно получить обоими способами, однако точность поковок будет различной. При объёмной штамповке (см. рис. 2, д) поковка представляет собой по существу, оттиск ручья. Инструмент при объёмной штамповке является специализированным, то есть предназначен для деталей одного наименования, например фланец воротниковый одного типоразмера. Форма и размеры поковки максимально приближены к форме и размерам фланца воротникового, для получения которого, как правило, требуется лишь незначительная механическая обработка (иногда обработка резаньем вообще не требуется для серийных специальных деталей).
а) | б) | |
---|---|---|
I | ![]() | ![]() |
II | ![]() | ![]() |
III | ![]() | ![]() |
Рис 4. Схемы изготовления нержавеющего воротникового фланца (а) и стального болта (б) способами ковки и объёмной штамповки: I – готовые детали, II – кованые поковки, III – штампованные поковки.
На рис. 4, а показан воротниковый фланец (I) из нержавеющей стали и поковки этой детали, полученные ковкой (II) и штамповкой(III). Для изготовления воротникового фланца кованную поковку механически обрабатывают по всей поверхности. Штампованную поковку фланца подвергают незначительной обработке резанием, а по некоторым поверхностям обработки не требуется. В данном случае расход дорогостоящего нержавеющего металла при применении ковки более, чем в три раза больше, чем при штамповке. На рисунке 4, б показан стальной нержавеющий болт с резьбой М36 (I) и поковки для его изготовления – кованная (II) и штампованная(III). Кованую поковку также обрабатывают по всей поверхности, а на штампованной требуется только нарезать резьбу.
Таким образом, изготовление деталей объёмной штамповкой требует значительно меньше расхода металла, чем ковкой. При обработке штампованных поковок сокращается трудоёмкость обработки резанием и расход режущего инструмента. Важным преимуществом объёмной штамповки является её высокая производительность (например, изготовление болта из нержавеющей стали штамповкой на горизонтально-ковочной машине или винтовом прессе возможно за один рабочий ход машины, в то время как при ковке для этого требуется до 10–15 ударов молота). Однако недостатком объёмной поковки является необходимость применения специального и сложного инструмента (штампов) для изготовления фланцев различных типоразмеров, что приводит к удорожанию этого процесса.
Достоинством ковки является возможность с помощью простого и недорогого инструмента изготовлять поковки разнообразной формы и любой массы – от самых маленьких (крепёжные изделия) до очень крупных фланцев сосудов и аппаратов. Однако ковка деталей, особенно сложной формы, требует высокой квалификации кузнеца.
Объёмную штамповку мы применяем в серийном производстве фланцев и крепежных изделий, там особенно необходимы высокая производительность и большая точность поковок. В этих условиях инструмент длительное время находится в эксплуатации, поэтому затраты на его изготовление окупаются.
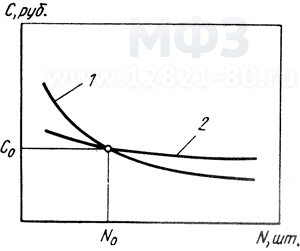
Рис 5. График зависимости себестоимости детали
от количества поковок в партии:
1 – при штамповке, 2 – при ковке.
Себестоимость, а следовательно, и цена фланцев и крепежных изделий, изготавливаемых из штампованных поковок, зависит от количества поковок в партии (рис. 5): с увеличением количества штампуемых поковок себестоимость детали заметно уменьшается (кривая 1); при ковке количество поковок в партии не оказывает такого заметного влияния на себестоимость детали (кривая 2). Точка пересечения кривых соответствует такому количеству деталей N0, изготовление которого и ковкой, и штамповкой даёт одинаковую себестоимость C0 при изготовлении партии, где N>N0, целесообразнее штамповка, при меньших объёмах производства экономически выгоднее ковка.
↑ В начало
Заключение
Объёмную штамповку обычно применяют в серийном и массовом производстве деталей трубопроводов, где особенно необходимы высокая производительность и большая точность поковок. В связи с тенденцией к увеличению серийности в машиностроении объёмная штамповка получает всё большее распространение.
↑ В начало
Список литературы
- Брюханов А.Н. Ковка и объёмная штамповка.. – М.: Машиностроение, 1975. – 408 c.
- Кузьминцев В.Н. Ковка на молотах и прессах.. – М.: Высшая школа, 1979. – 256 c.
- Бойцов В.В., Трофимов И.Д. Горячая объёмная штамповка : Учеб. для СПТУ. – 2-е изд., перераб. и доп.. – М.: Высш. шк., 1988. – 264 c.
- Охрименко Я.М Технология кузнечно-штамповочного производства : Учебник для вузов.. – М.: Машиностроение, 1976. – 560 c.
Получив доступ к данной странице, Вы автоматически принимаете Пользовательское соглашение.