Влияние радиуса впадины резьбы шпилек и болтов на надежность резьбовых крепежных соединений
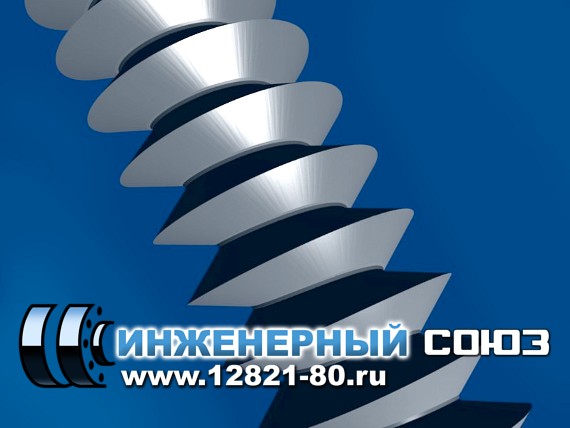
Резьба шпильки. Во впадинах резьбы крепежного изделия выполнено скругление.
При увеличении радиуса впадины резьбы шпилек и болтов предел выносливости соединений повышается. Однако в ряде опытов повышения прочности при увеличении радиуса впадины не обнаружено. Эксперименты позволяют повысить предел выносливости резьбовых крепежных соединений из стали, титановых и бериллиевых сплавов.
Дата публикации: 19 апреля 2011
Исследования влияния радиуса впадины резьбы на долговечность болтов
Первые эксперименты с болтами
Рис. 1. Кривые изменения работы удара
долговечности соединений при разных
радиусах впадины и внутренних диаметрах
резьбы M10
Первое экспериментальное исследование влияния радиуса впадины R резьбы на долговечность соединений выполнено Тумом и Штеделем. Они установили, что увеличение радиуса R от 0,1 до 0,2 мм для болтов М10 повышает в 2 раза работу удара W (рис. 1). Позднее А. И. Якушев исследовал зависимость сопротивления усталости соединений с болтами из стали 45 (σв - 720 МПа, σm = 140 МПа) и болтами из стали 40ХН2МА σв - 1300 МПа, σm-250 МПа) от радиуса впадины резьбы (табл. 1).
Из анализа приведенных данных следует, что при увеличении R предел выносливости соединений повышается. Однако в ряде опытов повышения прочности при увеличении отношения R/P не обнаружено. Это связано, по-видимому, с различными значениями остаточных напряжений во впадинах резьбы при неконтролируемых режимах нарезания.
Таблица 1
Резьба | Материал болта (сталь) | σап,МПа при R/P | ||||
0 | 0.108 | 0.144 | 0.216 | |||
M6 | 40XH2MA | 95 | 120 | 125 | ||
45 | ||||||
M12X1.5 | 40XH2MA | 80 | 90 | 90 | 115 | |
45 | 65 | 70 | 80 | 110 | ||
M24X1.5 | 45 | 50 | 60 | - |
Результаты исследований впадин резьбы крепежа западными лабораториями
В работе Р. Спроута, а также в исследованиях авторов установлено существенное влияние радиуса впадины на долговечность соединений. Подобные результаты для титановых и стальных болтов получены в одной из лабораторий США.
Сопфит и Филд исследовали сопротивление усталости болтовых соединений с резьбой 3/4" — 10 (d = 19 мм, Р = 2,54 мм) из марганцево-молибденовой и углеродистой сталей при R = (0,069... 0,145) Р. Результаты испытаний приведены в табл. 2.
Таблица 2
Материал болта | Способ изготовления резьбы | α,° | R,мм | σап, МПа |
Марганцево-молибденовая сталь (σв=984MПа) | Шлифование | 60 | 0,368 | 103,5 |
0,282 | 89,5 | |||
0,175 | 88,0 | |||
55 | 0,348 | 98,5 | ||
0,272 | 88,0 | |||
0,168 | 79,0 | |||
Накатывание | 60 | 0,356 | 219,5 | |
0,264 | 161,5 | |||
55 | 0,348 | 176,0 | ||
0,256 | 154,5 | |||
Углеродистая сталь (σв=614MПа) | Нарезание | 60 | 0,374 | 60,0 |
0,280 | 56,0 | |||
0,190 | 61,5 | |||
55 | 0,348 | 56,0 | ||
0,269 | 44,0 | |||
0,173 | 56,0 | |||
Накатывание | 60 | 0,343 | 121,5 | |
0,254 | 114,0 | |||
0,180 | 114,0 | |||
55 | 0,302 | 98,5 | ||
0,246 | 123,0 | |||
0,165 | 125,0 |
Данные показывают, что при увеличении радиуса R прочность соединений крепежа возрастает. В некоторых опытах наблюдалось обратное: увеличение отношения R/P приводило к снижению предела выносливости.
Это можно объяснить влиянием технологии изготовления (режимов нарезания или накатывания резьбы, обусловливающих различный наклёп в поверхностных слоях).
Отметим, что в указанных выше работах изучен сравнительно узкий диапазон изменения радиуса впадины.
Влияние радиуса впадины на сопротивление усталости крепежных изделий
Между тем, дальнейшее увеличение радиуса открывает большие возможности для повышения предела выносливости резьбовых крепежных соединений из стали и особенно из титановых и бериллиевых сплавов.
И. А. Биргер совместно с Ж. А. Ардеевым и Ю. Г. Рысем исследовали влияние радиуса впадины на сопротивление усталости соединений в связи с технологией изготовления и термической обработкой крепежных деталей (болтов, шпилек). Испытывали соединения шпилек и гаек с разным профилем резьбы М10; М10х0,75; М10Х1; М10X 1,25; М16Х1,5; М16Х2 (рис. 2).
Исследованные профили резьбы шпилек и болтов. Методы производства гаек для исследований.
Рис. 2. Профили резьбы
Резьба с профилем / представляла собой обычную метрическую резьбу по ГОСТ 9150—81, в соответствии с которым форма впадины может выполняться как плоскосрезанной, так и закругленной, причем радиус впадины относится к неконтролируемым параметрам резьбы.
Стандарт допускает также некоторое неконтролируемое закругление впадины до Rmax = 0,144Р, связанное с изнашиванием резьбообразующего инструмента. Резьба данного типа имела R = 0,12Р.
Резьба с профилем II отличалась от предыдущей наличием плоскосрезанной впадины (R = 0). Такая резьба широко применяется в малонагруженных резьбовых деталях из сталей.
Резьба с профилем III имела радиус впадины R = 0,2Р, близкий к рекомендуемому R = 0,18Р. Эта резьба служит основной для титановых крепежных деталей в авиационной и ракетной промышленности США, Франции, Великобритании и ФРГ. Кроме того, резьба крепежных изделий с таким профилем применяется за рубежом для болтов из тугоплавких ниобиевых и танталовых сплавов, а также для болтов из бериллиевых сплавов.
Рис. 3. Зависимость предела выносливости
соединений от радиуса впадины:
1- соединения с минимальными
зазорами в резьбе,
2 - соединения с увеличенными зазорами
Радиус R = 0,2Р является наибольшим, при котором обеспечивается частичная взаимозаменяемость с болтами, имеющими стандартный профиль резьбы.
Профиль IlIa резьбы шпильки идентичен профилю III, а резьба гайки соответствовала ГОСТ 9150—81, поэтому для обеспечения полной взаимозаменяемости шпилек и гаек зазор по внутреннему диаметру увеличили до 80 мкм. Резьба с профилем IV имела радиус впадины R =0,ЗР.
Наружный диаметр резьбы соответствовал ГОСТ 9150—81. Зазор по условному среднему диаметру, равному полусумме наружного и внутреннего диаметров резьбы, находился в пределах допусков, соответствующих посадке 4H/4h. Отметим, что резьба с R = 0,268Р применяется рядом авиационных фирм США для высоконагруженных болтов из титановых сплавов.
Резьба с профилем IVa также имела R = 0,ЗР, но в соединении использовалась стандартная гайка с резьбой по ГОСТ 9150—81.
Резьба с профилем V имела R = 0,4Р - минимальные зазоры по условному среднему диаметру соответствовали ГОСТ 16093—81. Резьба шпильки с профилем Va имела такой же радиус, но при производстве гаек резьба изготавливалась в соответствии с ГОСТ 9150—81.
Профиль VI резьбы был аналогичен профилю V, но в этом случае резьба имела плоскосрезанную впадину. Профиль VII гайки резьбы не отличался от профиля V, а профиль резьбы шпильки совпадал с профилем II.
Изготовление шпилек и гаек для проведённых исследований
Рис. 4. Соединения с незагруженной (в центре) резьбой
Изготовление шпилек осуществлялось из сталей 38ХА (σв = 1150 МПа), З0ХГСА (σв = 1650 МПа) и титанового сплава ВТ9 (σв = 1150 МПа).
Термообработку одной партии шпилек проводили до изготовления резьбы, шпильки другой партии подвергали термообработке после изготовления резьбы. Термическая обработка во втором случае снимала остаточные напряжения от механической обработки.
Гайки изготовляли из стали 45 (σв= 95 МПа) и титанового сплава ВТ9 (σв = 1150 МПа). Резьбу гаек нарезали метчиками, размеры резьбы контролировали десятью пробками со средними диаметрами от d2п = d2 — 0,005 мм до d2п = d2 + 0,105 мм. Для испытаний отбирали гайки с минимальными зазорами Δd.
Резьбу на шпильках одной партии нарезали на токарно-винторезном станке резцами с пластинами из твердых сплавов Т15К6 и ВК6, заточенными на оптикошлифовальном станке. Профиль резьбы шпилек контролировали с помощью инструментального микроскопа. Резьба на шпильках второй партии накатывалась на резьбонакатном станке при неизменном режиме. Размеры резьбы шпилек измеряли с применением инструментального микроскопа. Испытания проводили на машине резонансного типа с частотой 90 ... 98 Гц. Результаты испытаний представлены, на рис. 3. и в табл. 3.
Таблица 3
σm/σт | σап,МПа при R/P | |||||
0 | 0.12 | 0.20 | 0.30 | 0.40 | ||
0.2 | - | 165(155) | 185(185) | - | 150 | |
0.4 | 95 | 110(60) | 125(95) | 110 | 100 | |
0.7 | 55 | 75(40) | 85(60) | 95 | 100 | |
0.9 | - | 75 | 85 | - | 100 |
Примечание:
1. Резьба М10 накатана на термообработанных заготовках.
2. В скобках приведены данные для соединений из сплава ВТ9 (σв=1150 МПа).
Место разрушения шпильки
Установлено, что разрушение резьбовых соединений всегда происходило во впадине между первым и вторым рабочими витками резьбы шпилек. Усталостная трещина зарождалась, как правило, вблизи начала перехода от дуги впадины радиуса к прямолинейному участку, что свидетельствовало о существенной концентрации напряжений от изгиба витков.
Результаты исследований сопротивления усталости образцов с ненагруженными рабочими гранями витков (рис. 4) подтвердили вывод о превалирующем влиянии концентрации напряжений от изгиба над концентрацией напряжений от растяжения.
Предел выносливости таких образцов в 3 раза выше, чем для резьбовых соединений с одинаковой геометрией резьбы.
С увеличением радиуса впадины резьбы концентрация напряжений уменьшается и прочность соединений существенно возрастает (см. рис. 3).
Например, при переходе от резьбы с плоской впадиной (профиль II на рис. 2) к резьбе с R = 0,1P (профиль I) при dx = idem предел выносливости увеличивается на 23 %. В случае перехода от плоской впадины (профиль VI) к резьбе с R = 0,4Р (профиль V) при d1 = idem предельная амплитуда цикла возрастает в 2,25 раза.
Влияние диаметральных зазоров на сопротивление крепежных соединений усталости
Сопротивление усталости соединений с увеличенными диаметральными зазорами в резьбе существенно ниже сопротивления усталости соединений с минимальными зазорами, что подтверждают также данные для соединений из стали 38X А.
Отметим, что уменьшение перекрытия витков (за счет увеличения диаметра отверстия в гайке под резьбу) приводит х некоторому увеличению σап. Это можно объяснить повышением податливости витков болта и, как следствие, более благоприятным распределением нагрузки между витками резьбы.
Влияние термообработки заготовки перед накатыванием резьбы на крепеж
Рис. 5. Приращение предела
выносливости и пластической
деформации при накатывании
резьбы от радиуса впадины
В случае накатывания резьбы на термообработанных заготовках (без последующей термообработки шпилек) при R/P > 0,2 предел выносливости снижается. Это связано с уменьшением значений компонентов напряжений сжатия в резьбе от накатывания или нарезания. На рис. 5 приведены кривые изменения приращения σап и степени пластической деформации δ при накатывании резьбы в зависимости от радиуса впадины. Значение δ, %, можно вычислить по формуле
δ = (dc-d1)/dc100,
где d1 — внутренний диаметр резьбы; dc — диаметр стержня шпильки (болта) под накатывание резьбы.
Рис. 6. Кривые изменения микротвердости во впадинах
резьбы
M10 шпилек из стали 38XA: 1— R = 0; 2 — R = 0,18 мм;3 — R = 0,3 мм;
4 — R =0,46 мм; 5 — R= 0,6 мм; 6—R = 0,3 мм, после термообработки
Аналогичный характер имеет кривая изменения микротвердости во впадинах резьбы для шпилек с разными радиусами (рис. 6.).
Однако при напряжении предварительной затяжки σ0≥ 0,5σт напряжения сжатия, вызванные накатыванием, большей частью компенсируются напряжениями растяжения от затяжки.
Таким образом, при σ0≥ 0,5σт предел выносливости также возрастает с увеличением отношения R/P. Значения σап при разных средних напряжениях и радиусах впадины резьбы приведены в табл. 3.
Рис. 7. Зависимость несущей способности крепежа от
радиуса впадины:
1— соединения с зазорами в резьбе, соответствующими
посадке 6H/6G;
2 — то же с увеличенными зазорами в резьбе
Испытания резьбы крепежных изделий на прочность
Наряду с испытаниями на усталость для оценки влияния радиуса впадины витков проведены испытания на прочность. Испытывали соединения шпилек из стали 39XA и гаек из стали 45 с резьбой М10. Результаты испытаний представлены на рис. 7 (светлые точки соответствуют разрушению витков резьбы крепежных изделий, темные — обрыву стержня по резьбе) .
Анализ показывает, что при R > 0,ЗР предел прочности соединений снижается (в большей степени для мелких резьб).
Это связано с уменьшением перекрытия витков и увеличением концентрации напряжений в наиболее нагруженных сечениях витков. Однако сила, разрушающая резьбу в соединениях с R = 0,ЗР и Н = 0,8d, практически не отличается от силы, разрушающей стержень шпильки с резьбой по ГОСТ 9150—81. Прочность резьбовых соединений с увеличенными радиусами впадины можно повысить, увеличив высоту гайки до Н = 1,2d. В динамически нагруженных соединениях радиус впадины резьбы целесообразно увеличить до R = 0,2Р.
Конструктивный способ увеличения радиуса впадины резьбы крепежа
Рис. 8. Специальный профиль крепежной резьбы M10
Один из конструктивных вариантов резьбы с большим радиусом впадины показан на рис. 8. Предел выносливости рассматриваемой резьбы, без уменьшения перекрытия витков, примерно в 2 раза больше предела выносливости обычной метрической резьбы.
Предел выносливости рассматриваемой резьбы, без уменьшения перекрытия витков, примерно в 2 раза больше предела выносливости обычной метрической резьбы. Однако резьба с таким радиусом впадины сложна в изготовлении при производстве крепежа. При ее изготовлении необходимо тщательное выполнение переходов от закругления к прямолинейной части. Простое увеличение радиуса более приемлемо, хотя также требует тщательного выполнения этого перехода.
Список литературы
- Якушев А. И., Мустаев Р. Х., Мавлютов Р. Р. Повышение прочности и надежности резьбовых соединений.. – М. : Машиностроение, 1979. – 214 c.
- Якушев А. И. Влияние технологии изготовления и основных параметров резьбы на прочность резьбовых соединений.. – М. : Оборонгиз, 1956.
- Sproat R. Z., Walker R. A. Radiused-root threads-are they realey better // Assembly Engng. 1965. N 4..
Получив доступ к данной странице, Вы автоматически принимаете Пользовательское соглашение.